In the vast world of materials, few substances offer the remarkable versatility and transformative power of resin. From ancient natural secretions used for preservation to modern synthetic compounds revolutionizing industries, resin has a rich history and an even richer future. Among its many forms, one stands out for its exceptional strength, durability, and aesthetic appeal: epoxy resin. This remarkable polymer has moved beyond its industrial origins to become a staple in everything from high-performance coatings to intricate artistic creations, captivating both professionals and hobbyists alike.
Understanding epoxy resin means delving into its unique chemical composition, its impressive properties, and the myriad ways it can be applied. Whether you're a seasoned artisan, a DIY enthusiast, or simply curious about the materials that shape our modern world, exploring the depths of epoxy resin will reveal a fascinating realm of possibilities. This guide aims to demystify this powerful material, offering a comprehensive look at what makes it so special and how it continues to push the boundaries of innovation.
Table of Contents
- What is Resin? A Foundational Understanding
- Delving into Epoxy Resin: A Polymer Powerhouse
- The Science Behind Epoxy: How It Works
- Key Properties of Epoxy Resin
- Diverse Applications of Epoxy Resin
- Choosing the Right Epoxy Resin
- Working with Epoxy Resin: Best Practices
- The Future of Epoxy Resin
What is Resin? A Foundational Understanding
Before we immerse ourselves in the specifics of epoxy resin, it's essential to grasp the broader concept of resin itself. At its core, resin is a material composed of natural or synthetic polymers. These polymers, large molecules made of repeating structural units, can vary significantly in their chemical composition depending on the type of resin. Historically, the term "resin" (from the Latin resīna) referred to a viscous or solid substance naturally obtained from the organic secretions of certain plants, particularly coniferous trees like pines.
These natural resins, often formed in specialized resin canals within the plant, serve a crucial protective function. When a tree suffers an injury to its bark, resin slowly oozes out, acting as a natural bandage. This secretion protects the plant from insects and pathogens, repelling herbivores and preventing microbial invasion. Chemically, these natural resins are complex mixtures of carboxylic acids, terpenes, and essential oils, characterized by their extremely nonpolar nature due to their large molecular chains. This natural origin highlights resin's inherent versatility and protective qualities, qualities that modern synthetic resins aim to replicate and enhance. Today, while natural resins still have their place, the focus often shifts to synthetic varieties, which can be engineered for specific applications, including the remarkable material we know as epoxy resin.
Delving into Epoxy Resin: A Polymer Powerhouse
Among the vast array of synthetic resins, epoxy resin stands out as a true marvel of modern chemistry. Also known simply as "epoxy," or sometimes referred to as "porcelain" or "liquid crystal" due to its finished appearance, epoxy resin is a thermoset polymer. This means it undergoes an irreversible chemical reaction when mixed with a hardener or catalyst, transforming from a liquid state into a rigid, solid material. Unlike thermoplastics that can be melted and reshaped, thermoset polymers like epoxy become permanently hardened once cured.
Derived primarily from petroleum, epoxy resin is characterized by its exceptional hardness, remarkable durability, and often a brilliant, high-gloss finish. Its unique chemical structure, specifically the presence of epoxide functional groups (hence "epoxy"), allows it to form strong, cross-linked bonds during the curing process. This inherent strength and versatility make epoxy resin a go-to material for a wide array of projects, ranging from heavy-duty industrial applications to delicate artistic endeavors. Its ability to combine aesthetic appeal with unparalleled functionality has cemented its place as a revolutionary material in both industry and creative fields.
The Science Behind Epoxy: How It Works
The magic of epoxy resin lies in its fascinating chemical transformation. At its core, epoxy resin is a two-part system, typically consisting of a resin component and a hardener component. The resin itself is a reactive prepolymer or polymer containing those crucial epoxide groups. The hardener, often an amine, acts as a catalyst, initiating a chemical reaction when mixed with the resin. This reaction is an exothermic polymerization process, meaning it generates heat as it proceeds.
When the two components are combined in precise ratios (commonly 1:1 or 2:1 by volume, though this varies by product), the epoxide groups in the resin react with the amine groups in the hardener. This reaction creates strong covalent bonds, forming a dense, cross-linked polymer network. This network is what gives cured epoxy its characteristic strength, rigidity, and resistance to various environmental factors. The curing process can take anywhere from a few hours to several days, depending on the specific formulation, ambient temperature, and humidity. Understanding this fundamental chemical reaction is key to successfully working with epoxy resin, as proper mixing and environmental conditions are paramount for achieving optimal results and the desired properties like superior adhesion and durability.
Key Properties of Epoxy Resin
The widespread adoption of epoxy resin across countless industries and creative pursuits is directly attributable to its outstanding array of properties. These characteristics make it a preferred choice over many other materials for demanding applications.
- High Resistance and Durability: Epoxy resin is renowned for its exceptional resistance to a variety of stressors. Once cured, it forms a hard, robust surface that can withstand significant wear and tear, impacts, abrasion, and chemical exposure. This makes it ideal for environments where longevity and resilience are critical. Its durability is a primary reason it's used in industrial flooring and protective coatings.
- Superior Adhesion: One of epoxy's most celebrated qualities is its incredible adhesive strength. It forms strong bonds with a vast range of substrates, including concrete, wood, metals, plastics, and ceramics. This makes it an excellent choice for structural adhesives, sealants, and coatings that require strong, lasting bonds. In fact, epoxy resins are classified as structural or engineering adhesives, alongside polyurethanes, acrylics, and cyanoacrylates, due to their impressive bonding capabilities.
- Hardness and Brilliance: Cured epoxy resin typically exhibits a high degree of hardness, making it resistant to scratches and indentations. Coupled with its ability to cure to a crystal-clear, high-gloss finish, it creates surfaces that are not only functional but also aesthetically pleasing. This characteristic is particularly valued in art, jewelry making, and decorative flooring, where a "porcelain" or "glass-like" appearance is desired.
- Water and Chemical Resistance: The dense, cross-linked structure of cured epoxy makes it highly resistant to water, moisture, and a wide range of chemicals, including acids, alkalis, solvents, and oils. This property is invaluable in marine applications, industrial settings, and laboratories where exposure to corrosive substances is common.
- Electrical Insulation: Epoxy resin is an excellent electrical insulator. This property makes it indispensable in the electronics industry for encapsulating sensitive components, potting transformers, and insulating circuit boards, protecting them from environmental factors and electrical shorts.
- Low Shrinkage: During the curing process, epoxy resin exhibits very low shrinkage compared to many other polymers. This minimal volumetric change ensures that the cured material maintains its shape and dimensions accurately, which is crucial for precision applications and structural integrity.
These combined properties underscore why epoxy resin is such a versatile and indispensable material in modern manufacturing, construction, and creative fields.
Diverse Applications of Epoxy Resin
The remarkable properties of epoxy resin have led to its adoption across an astonishingly wide spectrum of applications. What began with purely industrial purposes has blossomed into a material that seamlessly combines aesthetics with functionality, touching nearly every aspect of our daily lives.
Epoxy in Industrial Settings
Epoxy resin's journey largely began in industrial environments, where its superior strength, durability, and chemical resistance were highly sought after.
- Adhesives and Sealants: As mentioned, epoxy resins are considered structural adhesives due due to their exceptional bonding strength. They are used to bond dissimilar materials, repair cracks in concrete, and seal joints in construction. From aerospace components to automotive parts, epoxy adhesives provide robust and long-lasting connections.
- Protective Coatings: Epoxy coatings are extensively used to protect surfaces from corrosion, abrasion, and chemical attack. This includes industrial floors, pipelines, storage tanks, and marine vessels. Their ability to form a hard, impermeable barrier significantly extends the lifespan of underlying materials.
- Electronics and Electrical Components: Given its excellent electrical insulation properties, epoxy is crucial in the electronics industry. It's used for encapsulating microchips, potting transformers, and creating printed circuit boards (PCBs), protecting delicate components from moisture, dust, and vibration.
- Tooling and Composites: Epoxy resins are key binders in the production of composite materials, such as fiberglass and carbon fiber. These composites are used in high-performance applications like aircraft, wind turbine blades, and sporting goods, where a combination of lightweight and high strength is required. Epoxy is also used to create molds, jigs, and fixtures for manufacturing processes due to its dimensional stability and hardness.
Epoxy in Art and Craft
Beyond its industrial prowess, epoxy resin has revolutionized the world of art and creation, becoming a favorite among artisans and DIY enthusiasts.
- Jewelry Making: Crystal clear art casting resin and hardener, often in a 1:1 mix ratio, are perfect for creating stunning, transparent jewelry. Epoxy allows for embedding various objects like dried flowers, glitter, or small trinkets, preserving them in a durable, no-yellowing, glass-like finish.
- Casting and Molds: Artists use epoxy for casting intricate shapes, figurines, and decorative objects. Its ability to capture fine details and cure to a solid form makes it ideal for creating unique pieces or replicating existing ones using silicone molds.
- Resin Art and Paintings: Epoxy is poured onto canvases or panels to create glossy, three-dimensional artworks. Artists manipulate pigments, glitters, and other media within the wet resin to produce mesmerizing abstract pieces, often mimicking the appearance of polished stone or liquid glass.
- Tabletops and Countertops: Epoxy is frequently used to create durable, high-gloss finishes on tabletops, countertops, and bar tops. It can encapsulate objects, create "river tables" with stunning visual effects, or simply provide a protective, easy-to-clean surface that resists spills and scratches.
Epoxy for Flooring and Surfaces
One of the most visible and impactful applications of epoxy resin is in flooring and surface coatings, where its durability and aesthetic appeal truly shine.
- Residential and Commercial Floors: Epoxy flooring has gained immense popularity for its seamless, high-gloss finish, often resembling polished porcelain. It's highly resistant to stains, chemicals, and heavy foot traffic, making it ideal for garages, basements, retail spaces, and even residential interiors seeking a modern, industrial look.
- Decorative Finishes: Beyond plain colors, epoxy can be mixed with metallic pigments, flakes, or aggregates to create stunning decorative effects like marbled patterns, metallic sheens, or terrazzo-like finishes. This allows for highly customizable and unique floor designs.
- Protective Overlays: For concrete and wood surfaces, epoxy acts as a protective overlay, enhancing their longevity and making them easier to clean and maintain. It seals porous materials, preventing moisture penetration and deterioration.
Other Innovative Uses
The versatility of epoxy resin continues to inspire new applications:
- Marine and Automotive Repairs: Its water resistance and strong adhesion make epoxy ideal for repairing boat hulls, surfboards, and automotive bodywork.
- 3D Printing: Certain types of epoxy resins are used in stereolithography (SLA) 3D printing, where UV light cures the liquid resin layer by layer to build complex, highly detailed objects.
- Sporting Goods: From skis and snowboards to tennis rackets and fishing rods, epoxy is integral in manufacturing high-performance sporting equipment due to its strength-to-weight ratio when combined with fibers.
The adaptability of epoxy resin, coupled with its robust characteristics, ensures its continued relevance and expansion into new and exciting fields.
Choosing the Right Epoxy Resin
With the diverse range of applications for epoxy resin, it's no surprise that various formulations exist, each tailored for specific needs. Selecting the correct type of epoxy is crucial for the success and longevity of your project. The primary distinctions often lie in their viscosity, cure time, UV resistance, and intended use.
- Casting Resins: These typically have a lower viscosity (thinner consistency), allowing them to flow easily into molds and release air bubbles more effectively. They often have longer cure times and are designed for thicker pours, making them ideal for jewelry, deep river tables, and embedding objects without excessive heat buildup. Look for terms like "crystal clear art casting resin."
- Coating Resins: These are generally thicker (higher viscosity) and designed to create a durable, high-gloss surface layer. They cure faster and are perfect for countertops, bar tops, and artwork where a protective, self-leveling finish is desired.
- UV Resistant Epoxies: While most epoxies will yellow over time when exposed to UV light, some formulations incorporate additives to slow down this process. If your project will be exposed to sunlight, investing in a UV-resistant epoxy is advisable to maintain clarity and prevent yellowing.
- Marine Epoxies: Specifically formulated for marine environments, these epoxies offer superior water resistance and adhesion to wood and fiberglass, making them ideal for boat building and repair.
- Industrial/Structural Epoxies: These are engineered for maximum strength, chemical resistance, and specific performance requirements in demanding industrial applications, often with specialized additives for heat or impact resistance.
Always check the manufacturer's specifications regarding mix ratios, pot life (working time), cure time, and recommended application thickness. Understanding these parameters will guide you in choosing the epoxy resin that best suits your project's demands.
Working with Epoxy Resin: Best Practices
While epoxy resin is a remarkably versatile material, working with it effectively requires adherence to certain best practices to ensure safety, achieve optimal results, and prevent common issues.
- Safety First: Always work in a well-ventilated area. Wear appropriate personal protective equipment (PPE), including nitrile gloves to protect your skin and safety glasses to protect your eyes. Some individuals may develop sensitivities or allergies to epoxy over time, so consistent protection is key. Refer to the product's Material Safety Data Sheet (MSDS) for specific safety guidelines.
- Accurate Measurement: Epoxy is a two-part system that relies on precise ratios for proper curing. Use accurate measuring cups or scales to ensure the resin and hardener are mixed exactly as specified by the manufacturer (e.g., 1:1 by volume, 2:1 by weight). Incorrect ratios can lead to sticky, soft, or brittle cures.
- Thorough Mixing: Once measured, mix the resin and hardener thoroughly. Scrape the sides and bottom of your mixing container to ensure all components are fully incorporated. Inadequate mixing is a common cause of soft spots or uncured areas. Mix slowly to avoid introducing excessive air bubbles.
- Temperature and Humidity Control: Epoxy cures best within a specific temperature range, typically around 70-75°F (21-24°C). Extreme temperatures can affect cure time and final properties. High humidity can also interfere with the curing process, especially with certain hardeners, leading to surface hazing or stickiness.
- Surface Preparation: Ensure your working surface and the substrate you're applying epoxy to are clean, dry, and free of dust, grease, or contaminants. Proper surface preparation is vital for achieving strong adhesion and a flawless finish.
- Bubble Management: Air bubbles can be a common issue, especially with thicker pours. Techniques like warming the resin slightly before mixing (to reduce viscosity), mixing slowly, and using a heat gun or torch (briefly and carefully) over the poured epoxy can help release trapped bubbles.
- Cure Time and Post-Cure: Respect the recommended cure times. While the epoxy may be tack-free after a few hours, it often takes several days to achieve full hardness and chemical resistance. Avoid placing heavy objects or exposing the project to harsh conditions until it is fully cured.
By following these guidelines, you can significantly improve your success rate when working with epoxy resin, ensuring beautiful, durable, and professional-looking results.
The Future of Epoxy Resin
The journey of epoxy resin, from its industrial beginnings to its current widespread use in art and everyday applications, is a testament to its enduring versatility and strength. But the evolution of this remarkable polymer is far from over. As technology advances and societal needs shift, the future of epoxy resin promises even more innovation and adaptation.
One significant area of focus is sustainability. Researchers are actively exploring bio-based epoxy resins derived from renewable resources, reducing reliance on petroleum-based feedstocks. Efforts are also being made to develop more environmentally friendly hardeners and formulations that produce fewer volatile organic compounds (VOCs). Recycling and repurposing cured epoxy, though challenging due to its thermoset nature, are also areas of ongoing research, aiming to create a more circular economy for these materials.
Furthermore, advancements in nanotechnology are leading to the development of enhanced epoxy resins with superior properties. Incorporating nanoparticles can improve scratch resistance, UV stability, electrical conductivity, or even introduce self-healing capabilities. Smart epoxies, which can change properties in response to external stimuli, are also on the horizon, opening doors for applications in advanced sensors, smart coatings, and responsive materials. The continued exploration of new curing mechanisms, faster cure times, and specialized additives will further broaden the scope of what epoxy resin can achieve. From more efficient manufacturing processes to even more durable and aesthetically pleasing consumer products, epoxy resin remains at the forefront of material science, continually pushing the boundaries of what's possible.
Conclusion
Epoxy resin is undeniably a material that has transformed countless industries and empowered a new generation of creators. We've explored its origins, understood its fundamental chemistry as a thermoset polymer derived from petroleum, and marveled at its incredible properties—from its unparalleled hardness and superior adhesion to its remarkable durability and brilliant finish. Its journey from an industrial workhorse to a beloved medium in art and design showcases its adaptability and enduring appeal.
Whether you're considering an epoxy floor for your garage, crafting unique jewelry, or embarking on a large-scale industrial project, understanding the nuances of this material is key. By adhering to best practices in mixing, application, and safety, you can harness the full potential of epoxy resin to achieve stunning and long-lasting results. The ongoing innovation in sustainable and high-performance formulations ensures that epoxy resin will continue to be a vital component in shaping our built environment and inspiring creative expression for years to come.
What are your experiences with epoxy resin? Share your thoughts, projects, or questions in the comments below! We'd love to hear how this versatile material has impacted your work or hobbies. If you found this guide helpful, consider sharing it with others who might benefit, and explore our other articles for more insights into the world of materials and craftsmanship.
Related Resources:
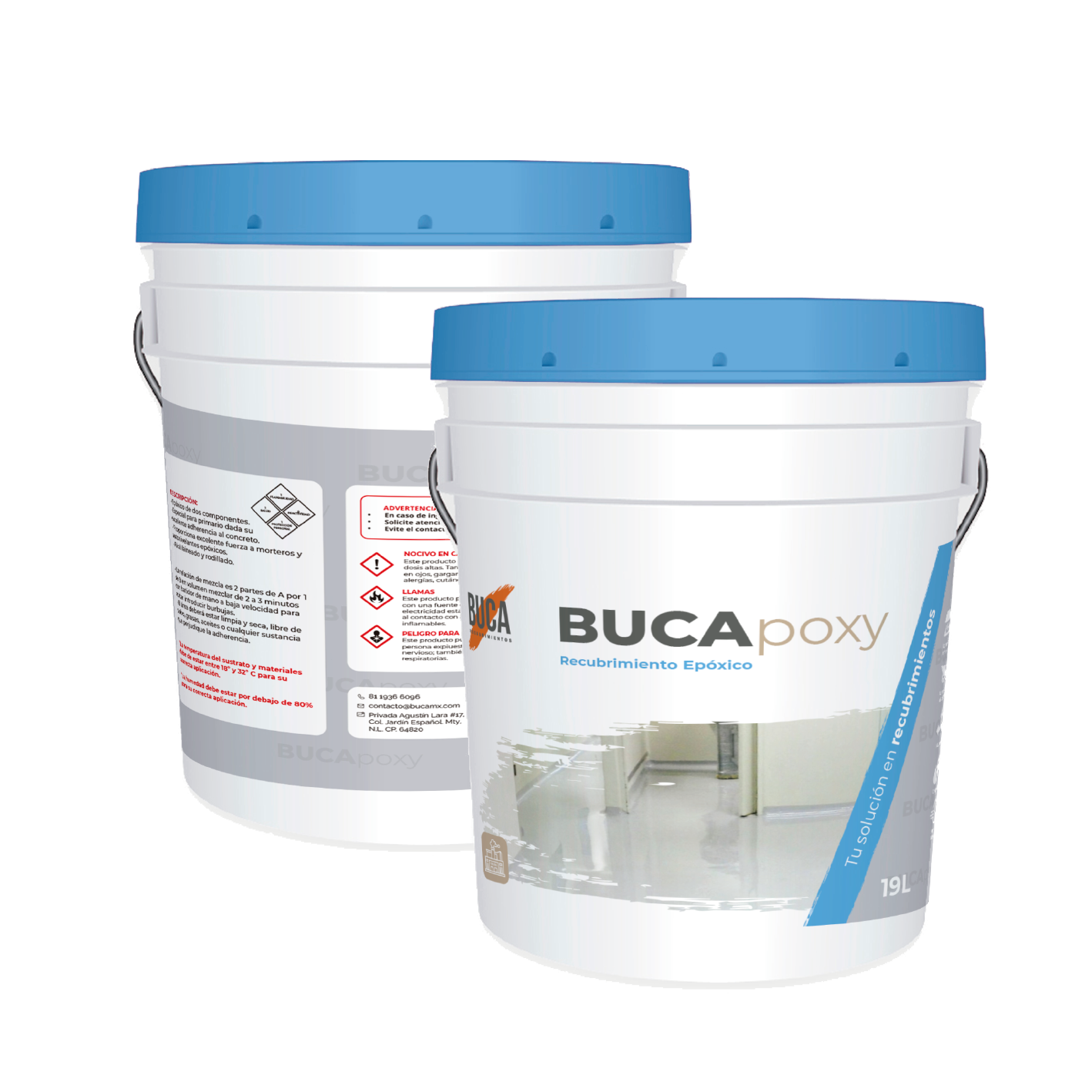
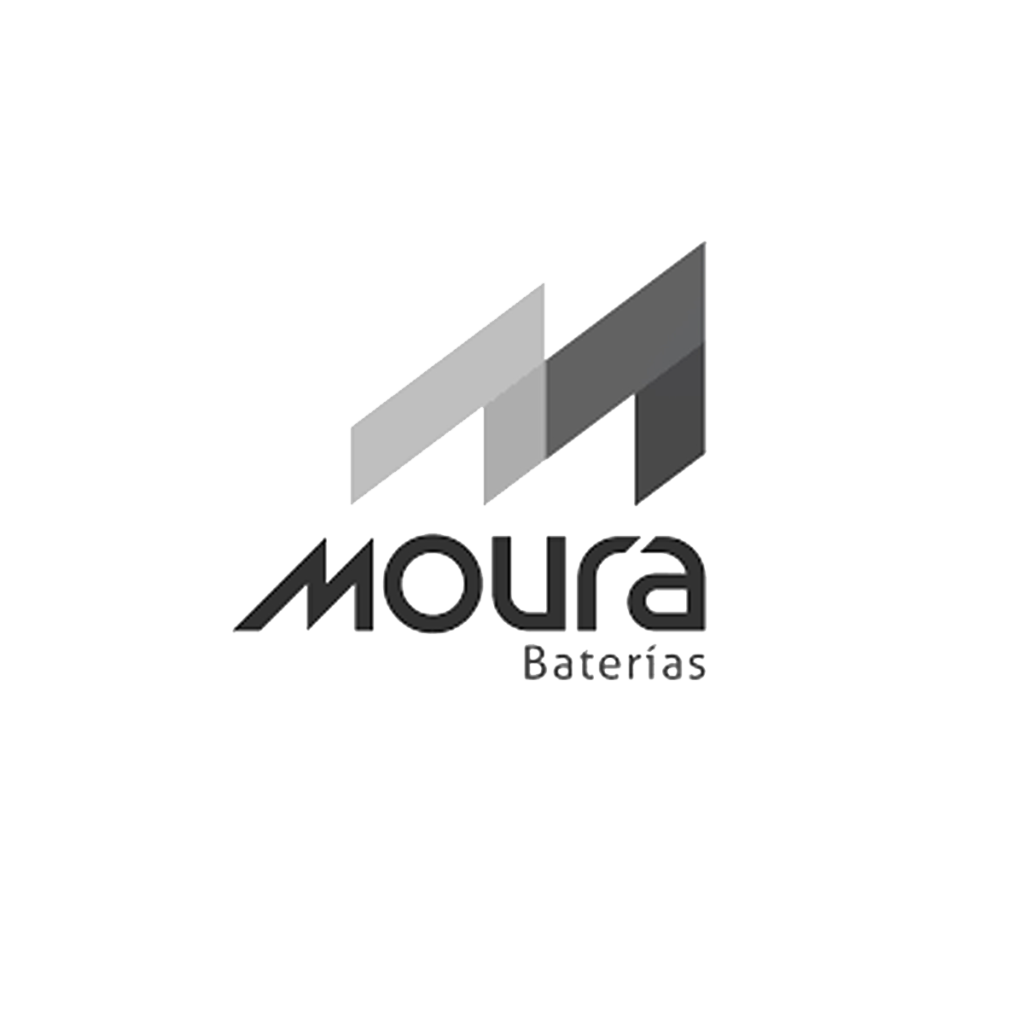
Detail Author:
- Name : Edna Bruen V
- Username : wgleason
- Email : yundt.trace@hotmail.com
- Birthdate : 1991-03-05
- Address : 445 Helena Freeway Schmittfurt, TN 09754-4526
- Phone : 775.527.1539
- Company : Sanford-Windler
- Job : Computer Specialist
- Bio : Et tempora non in quasi dolorum. Consequuntur ea eum nobis ipsam sed veniam dolorum sint. Officia iste fuga quidem.
Socials
twitter:
- url : https://twitter.com/myrtle_wehner
- username : myrtle_wehner
- bio : Et possimus laboriosam atque ad odio qui corporis facilis. Iure ullam culpa est cumque non voluptatem maxime commodi. Et saepe dignissimos quia.
- followers : 5508
- following : 2712
instagram:
- url : https://instagram.com/myrtle_xx
- username : myrtle_xx
- bio : Aut similique sit est ut. Quaerat est velit dolorum est optio. Pariatur ut qui distinctio totam et.
- followers : 759
- following : 492
facebook:
- url : https://facebook.com/myrtle_wehner
- username : myrtle_wehner
- bio : Eveniet exercitationem unde ullam eum doloremque a.
- followers : 2039
- following : 461
linkedin:
- url : https://linkedin.com/in/myrtlewehner
- username : myrtlewehner
- bio : Qui dolor amet adipisci quaerat.
- followers : 2886
- following : 1535