**In the realm of modern manufacturing, few acronyms carry as much weight and transformative power as CNC. Computer Numerical Control, or CNC, represents a pivotal leap in how products are made, moving from manual craftsmanship to highly precise, automated production.** It's a technology that underpins countless industries, from aerospace and automotive to medical devices and consumer electronics, fundamentally changing the speed, accuracy, and complexity with which parts can be created. Understanding the **CNC meaning** is crucial for anyone looking to grasp the intricacies of contemporary industrial processes. This comprehensive guide will demystify what CNC truly is, how it works, its historical roots, and why it has become an indispensable tool in the global manufacturing landscape. Prepare to delve into the fascinating world where computer code translates into tangible objects, pushing the boundaries of what's possible.
Table of Contents
- What is CNC Meaning? The Core Definition
- From NC to CNC: An Evolution of Control
- How CNC Machining Works: The Process Unveiled
- Key Components of a CNC System
- Types of CNC Machines: A Diverse Toolkit
- Materials and Applications: Where CNC Shines
- The Advantages of CNC Machining: Precision and Efficiency
- Challenges and Considerations in CNC Operations
- The Future of CNC: Smart Manufacturing
- Conclusion: The Enduring Impact of CNC
What is CNC Meaning? The Core Definition
At its heart, **CNC meaning** refers to "Computer Numerical Control." It is a sophisticated manufacturing method that automates the control, movement, and precision of machine tools through the use of preprogrammed computer software. Unlike older, manually operated machines, CNC systems interpret digital instructions to guide tools with incredible accuracy, performing tasks like cutting, carving, grinding, drilling, and milling. To elaborate, as the "Data Kalimat" states, "Computer numerical control (CNC) or CNC machining is the automated control of machine tools by a computer." This highlights the fundamental shift from human intervention to computer-driven precision. It's not just about a machine moving; it's about a computer dictating every single movement, every cut, every rotation, ensuring consistency and accuracy that human hands simply cannot replicate over extended periods. This level of automation is what makes CNC a cornerstone of modern industrial production, delivering unparalleled repeatability and quality.From NC to CNC: An Evolution of Control
To fully appreciate the **CNC meaning**, it's helpful to understand its lineage. Before Computer Numerical Control, there was simply Numerical Control (NC). The "Data Kalimat" accurately notes, "It is an evolution of numerical control (NC), where machine tools are directly" controlled. Early NC machines, developed in the 1940s and 50s, used punched tapes or cards containing numerical data to control machine movements. These tapes would dictate coordinates and operations, allowing for a degree of automation beyond manual control. However, NC systems were rigid. Changes required re-punching tapes, and their processing power was limited. The advent of computers revolutionized this. By integrating a dedicated computer into the control system, NC evolved into CNC. This transformation allowed for: * **Flexibility:** Programs could be easily edited, stored, and retrieved. * **Complexity:** More intricate geometries and multi-axis movements became feasible. * **Feedback Loops:** Computers could monitor tool position and adjust in real-time, significantly improving accuracy and reducing errors. * **Integration:** CNC machines could be linked to Computer-Aided Design (CAD) and Computer-Aided Manufacturing (CAM) software, streamlining the entire design-to-production workflow. This evolution from a rudimentary tape-driven system to a sophisticated computer-controlled one is central to the modern **CNC meaning**, signifying a leap from simple automation to intelligent, adaptable manufacturing.How CNC Machining Works: The Process Unveiled
The process of **CNC machining** might seem complex at first glance, but it can be broken down into several logical steps. The "Data Kalimat" states, "If this sounds even more confusing, don’t worry — the process is complex, but this guide will walk you through everything you need." Indeed, while the underlying technology is intricate, the workflow is quite straightforward once understood. Essentially, **CNC machining is a subtractive manufacturing process that utilizes computerized controls and machine tools to remove layers of material from a stock piece.** This means it starts with a solid block of material (the "stock piece" or "workpiece") and removes material to create the desired shape, as opposed to additive processes like 3D printing which build up material. Let's explore the key stages:Design and CAD/CAM
The journey begins with design. Engineers and designers use Computer-Aided Design (CAD) software to create a 2D or 3D model of the part they want to manufacture. This digital model serves as the blueprint. Once the design is finalized, it's imported into Computer-Aided Manufacturing (CAM) software. The CAM software is the bridge between the design and the machine. It takes the CAD model and translates it into specific instructions that the CNC machine can understand. This involves: * **Tool Path Generation:** Determining the precise path the cutting tool will take to remove material. * **Feeds and Speeds:** Calculating how fast the tool should move (feed rate) and how fast it should spin (spindle speed) for optimal material removal and surface finish. * **Tool Selection:** Specifying which tools (drills, end mills, etc.) are needed for different operations. This stage is critical as it directly influences the quality, efficiency, and cost of the final product.G-Code: The Language of Machines
Once the CAM software has generated all the necessary instructions, it outputs them in a specific programming language, most commonly G-code (Geometric Code) and M-code (Miscellaneous Code). As the "Data Kalimat" mentions, "CNC robotics turns code into motion." This code is a series of alphanumeric commands that tell the CNC machine exactly what to do: * **G-codes:** Define movements (e.g., G00 for rapid traverse, G01 for linear interpolation, G02/G03 for circular interpolation), specific operations (e.g., G81 for drilling cycle), and coordinate systems. * **M-codes:** Control miscellaneous functions like turning the spindle on/off, coolant on/off, tool changes, and program stops. This G-code program is then loaded into the CNC machine's control unit. It's essentially a highly detailed recipe for manufacturing the part, ensuring that every operation is executed with absolute precision.Execution and Monitoring
With the G-code loaded, the CNC machine is ready to operate. The operator secures the raw material onto the machine's work table. The CNC control unit then reads the G-code line by line, sending signals to the machine's motors (servos or steppers) to control the movement of its axes and the rotation of the spindle. During operation, the CNC system continuously monitors the machine's position and performance through feedback sensors. This closed-loop system ensures that if there's any deviation from the programmed path, the system can make real-time adjustments to maintain accuracy. This constant feedback is a key differentiator from older NC systems and a core aspect of the modern **CNC meaning** in terms of precision and reliability. The machine executes the program autonomously, removing material layer by layer until the final part is precisely formed according to the digital design.Key Components of a CNC System
A typical CNC system is a sophisticated integration of several interconnected components, all working in harmony to achieve automated machining. Understanding these components helps to grasp the full scope of **CNC meaning** in practice: * **CNC Machine Tool:** This is the physical machine that performs the cutting, drilling, or other operations. It could be a mill, lathe, router, grinder, or even a 3D printer. The "Data Kalimat" mentions, "It involves controlling machines like mills, lathes, routers..." These machines are equipped with multiple axes of motion (typically 3, 4, or 5, but sometimes more) that allow the cutting tool to move in various directions relative to the workpiece. * **Control Unit (Controller):** This is the "brain" of the CNC system. It's a dedicated computer that receives the G-code program, interprets it, and translates it into electrical signals that drive the machine's motors. Modern controllers often have graphical interfaces, simulation capabilities, and advanced error detection. * **Drive System (Motors and Amplifiers):** These components convert the electrical signals from the control unit into mechanical motion. Servo motors are commonly used for their precision and ability to maintain position under load, while stepper motors are found in simpler or smaller machines. Amplifiers boost the signals to power these motors. * **Feedback Devices (Encoders/Resolvers):** These sensors are attached to the machine's axes and motors. They continuously monitor the actual position and speed of the machine components and send this data back to the control unit. This feedback loop is crucial for ensuring accuracy and making real-time corrections, a testament to the precision inherent in the **CNC meaning**. * **Cutting Tools:** These are the specialized tools (e.g., end mills, drills, inserts) that physically remove material from the workpiece. The selection of the correct tool is critical for achieving the desired part geometry and surface finish. * **Workholding Devices:** These are clamps, vises, chucks, or fixtures used to securely hold the workpiece in place during machining. Stability is paramount to prevent vibration and ensure accurate cutting. Each of these components plays a vital role, contributing to the overall efficiency, accuracy, and versatility that defines **CNC meaning** in the industrial context.Types of CNC Machines: A Diverse Toolkit
The versatility of **CNC meaning** extends to the wide array of machine types it can control. While the core principle of computer-guided automation remains constant, the specific machine tools vary depending on the manufacturing process and the desired outcome. The "Data Kalimat" provides a good overview: "CNC stands for computer numerical control and refers to the automated control of machining tools, such as drills, lathes, mills, grinders, routers, and 3D printers, using a computer." Here are some of the most common types of CNC machines: * **CNC Mills:** Perhaps the most common type, CNC mills use rotating cutting tools to remove material from a stationary workpiece. They are highly versatile and can perform a wide range of operations, including drilling, boring, routing, and intricate contouring. They come in various configurations, such as 3-axis, 4-axis, and 5-axis machines, allowing for increasing complexity in part geometry. * **CNC Lathes (Turning Machines):** Unlike mills, lathes hold the workpiece and rotate it, while a stationary cutting tool removes material. They are ideal for creating cylindrical or conical parts, such as shafts, pins, and bushings. Modern CNC lathes often include live tooling capabilities, allowing for milling and drilling operations on the same machine. * **CNC Routers:** Similar to mills but typically larger and designed for softer materials like wood, plastics, composites, and some non-ferrous metals. CNC routers are widely used in signage, furniture making, and artistic applications. * **CNC Grinders:** These machines use abrasive wheels to achieve extremely fine surface finishes and tight tolerances on hardened materials. They are often used for finishing operations after initial machining. * **CNC Plasma Cutters:** These machines use a high-temperature plasma torch to cut through electrically conductive materials like steel, aluminum, and copper. They are fast and efficient for cutting large sheets of metal. * **CNC Laser Cutters:** Employing a high-powered laser beam, these machines precisely cut or engrave a wide range of materials, including metals, plastics, wood, and fabrics. They offer very high precision and minimal material distortion. * **CNC Waterjet Cutters:** These machines use a high-pressure stream of water, often mixed with abrasive particles, to cut through virtually any material, from soft foams to hard metals and ceramics, without generating heat. * **CNC 3D Printers (Additive Manufacturing):** While traditionally **CNC meaning** refers to subtractive processes, the term is increasingly applied to additive manufacturing. These machines build parts layer by layer from a digital design, controlling the deposition head with computer numerical control. Each type of CNC machine is optimized for specific tasks and materials, showcasing the broad applicability and adaptability of computer numerical control across the manufacturing spectrum.Materials and Applications: Where CNC Shines
The versatility of **CNC machining** extends beyond just the types of machines; it also encompasses the vast array of materials that can be processed and the diverse industries that benefit from this technology. Essentially, if a material can be cut, drilled, or shaped, there's likely a CNC machine capable of doing it. **Common Materials Processed by CNC:** * **Metals:** Aluminum, steel (stainless, carbon, alloy), brass, copper, titanium, nickel alloys. These are extensively used in aerospace, automotive, and heavy machinery. * **Plastics:** ABS, polycarbonate, nylon, acrylic, PVC, Delrin, PEEK. Ideal for prototypes, consumer goods, medical components, and electrical enclosures. * **Wood:** Hardwoods, softwoods, plywood, MDF. Utilized in furniture, cabinetry, architectural models, and artistic carvings. * **Composites:** Carbon fiber, fiberglass. Essential for lightweight, high-strength applications in aerospace, sports equipment, and automotive racing. * **Foams:** Urethane, polystyrene. Used for prototyping, insulation, and packaging. * **Exotic Materials:** Ceramics, glass, precious metals. Often found in specialized applications like medical implants, jewelry, and scientific instruments. **Key Applications Across Industries:** The impact of **CNC meaning** on various sectors is profound: * **Aerospace:** Manufacturing complex, high-precision components for aircraft engines, airframes, and landing gear, often from exotic metals, where tolerances are extremely tight and reliability is paramount. * **Automotive:** Producing engine blocks, transmission parts, custom wheels, molds for body panels, and intricate interior components. CNC enables rapid prototyping and mass production with consistent quality. * **Medical & Dental:** Creating surgical instruments, prosthetics, implants (e.g., hip and knee replacements), dental crowns, and custom aligners. The precision and biocompatibility requirements make CNC indispensable. * **Electronics:** Machining enclosures for electronic devices, heat sinks, and circuit board components. * **Consumer Goods:** Manufacturing parts for appliances, sporting goods, toys, and custom furniture. * **Tool & Die Making:** Producing highly accurate molds, dies, and fixtures used in injection molding, stamping, and other manufacturing processes. * **Robotics & Automation:** Creating precise components for robotic arms, automated assembly lines, and other industrial machinery. As the "Data Kalimat" states, "CNC robotics turns code into motion," directly linking CNC to the broader automation trend. The ability of CNC machines to work with such a broad spectrum of materials and deliver unparalleled precision makes them a cornerstone of modern industrial production, driving innovation and efficiency across virtually every manufacturing sector.The Advantages of CNC Machining: Precision and Efficiency
The widespread adoption of **CNC machining** isn't merely a trend; it's a testament to the significant advantages it offers over traditional manufacturing methods. These benefits directly contribute to improved product quality, reduced costs, and faster time-to-market. Understanding these advantages is key to grasping the full scope of **CNC meaning** in a competitive global economy. 1. **High Precision and Accuracy:** This is arguably the most significant advantage. CNC machines can achieve tolerances of just a few microns, far exceeding what is possible with manual machining. The computer control eliminates human error and fatigue, ensuring that every part produced is identical to the digital design. This is critical for industries like aerospace and medical, where even tiny deviations can have catastrophic consequences. 2. **Repeatability and Consistency:** Once a program is created and verified, a CNC machine can produce thousands, even millions, of identical parts without any variation. This consistency is vital for mass production and for maintaining product quality across batches. 3. **Increased Production Speed:** CNC machines operate continuously and at optimal speeds and feeds, leading to significantly faster production cycles compared to manual methods. They can run 24/7 with minimal supervision, maximizing output. 4. **Reduced Labor Costs:** While skilled operators are still needed for programming, setup, and oversight, CNC machines reduce the need for constant human intervention during the machining process itself. One operator can often manage multiple machines, leading to lower labor costs per part. 5. **Enhanced Safety:** Automation reduces the direct interaction between human operators and dangerous machinery, minimizing the risk of accidents and injuries in the workplace. 6. **Versatility and Flexibility:** As discussed, CNC machines can work with a vast array of materials and perform diverse operations. Changing from one part to another simply requires loading a new program and potentially changing tools, making them highly adaptable for varied production runs. 7. **Complex Geometries:** CNC machines, especially those with multiple axes (4-axis, 5-axis), can create highly intricate and complex shapes that would be impossible or extremely difficult to achieve with manual methods. This opens up new possibilities for product design and innovation. 8. **Reduced Waste and Material Optimization:** The precision of CNC machining leads to less material waste. Programs can be optimized to utilize raw materials efficiently, contributing to cost savings and environmental benefits. 9. **Prototyping and Rapid Iteration:** CNC is excellent for quickly producing prototypes. Designers can rapidly test and refine designs, accelerating the product development cycle. These advantages collectively underscore why **Computer Numerical Control** has become an indispensable technology, driving efficiency, quality, and innovation across the manufacturing sector.Challenges and Considerations in CNC Operations
While the advantages of **CNC machining** are numerous and transformative, it's also important to acknowledge the challenges and considerations associated with its implementation and operation. A comprehensive understanding of **CNC meaning** includes recognizing both its strengths and its limitations. 1. **Initial Investment Cost:** CNC machines, especially advanced multi-axis models, represent a significant capital investment. The cost of the machinery itself, along with necessary software (CAD/CAM) and tooling, can be substantial, making it a barrier for very small businesses. 2. **Programming Complexity:** While user-friendly interfaces are improving, generating efficient and error-free G-code programs still requires specialized knowledge and training. Complex parts demand highly skilled programmers. Errors in programming can lead to costly material waste, tool breakage, or even machine damage. 3. **Maintenance and Downtime:** Like any sophisticated machinery, CNC machines require regular maintenance to ensure optimal performance and longevity. Unexpected breakdowns can lead to costly downtime, impacting production schedules and profitability. Specialized technicians are often needed for repairs. 4. **Tooling Costs and Management:** Different materials and operations require specific cutting tools. These tools wear out and need to be replaced, representing an ongoing operational cost. Effective tool management, including inventory and regrinding, is crucial. 5. **Material Handling and Setup Time:** While the machining process itself is automated, the loading and unloading of raw materials and finished parts, as well as the setup of workholding devices, still require human intervention. For small batch sizes, setup time can significantly impact overall efficiency. 6. **Environmental Considerations:** The machining process generates chips and swarf, and coolant fluids are often used. Proper disposal and recycling of these byproducts are important environmental considerations. Energy consumption of large machines can also be a factor. 7. **Skill Gap:** While direct labor is reduced, there's a growing demand for highly skilled CNC programmers, operators, and maintenance technicians. Finding and retaining such talent can be a challenge for manufacturers. Addressing these challenges often involves strategic planning, investing in training, implementing robust maintenance schedules, and continuously optimizing processes. Despite these considerations, the overwhelming benefits of **Computer Numerical Control** continue to drive its widespread adoption and innovation in manufacturing.The Future of CNC: Smart Manufacturing
The evolution of **CNC meaning** is far from over. As technology continues to advance, the future of **CNC machining** is increasingly intertwined with broader trends in smart manufacturing, Industry 4.0, and the Industrial Internet of Things (IIoT). These developments promise to make CNC operations even more efficient, autonomous, and integrated. * **Increased Automation and Robotics Integration:** We will see more seamless integration of CNC machines with robotic arms for automated material loading/unloading, tool changing, and post-machining operations. This moves towards fully lights-out manufacturing, where human intervention is minimal. * **Artificial Intelligence (AI) and Machine Learning (ML):** AI and ML algorithms are beginning to optimize CNC processes. They can analyze sensor data to predict tool wear, adjust cutting parameters in real-time for optimal performance, detect anomalies, and even generate more efficient G-code. This leads to predictive maintenance and adaptive manufacturing. * **Cloud-Based CNC and Remote Monitoring:** The ability to monitor and even control CNC machines remotely via cloud platforms is becoming more common. This allows for better oversight of global operations, real-time performance analytics, and quicker troubleshooting. * **Additive Manufacturing Integration:** The lines between subtractive (CNC machining) and additive (3D printing) manufacturing are blurring. Hybrid machines that can both add and remove material are emerging, offering unprecedented design freedom and manufacturing flexibility. This expands the traditional **CNC meaning** to encompass a wider range of fabrication methods. * **Advanced Simulation and Digital Twins:** Sophisticated simulation software will allow for even more accurate virtual prototyping and process optimization before any material is cut. Digital twins – virtual replicas of physical machines and processes – will enable real-time monitoring, predictive analysis, and optimization of entire production lines. * **Sustainable Manufacturing:** Future CNC systems will likely focus more on energy efficiency, reducing material waste further, and utilizing more sustainable coolants and lubricants. * **Human-Machine Collaboration (Cobots):** Collaborative robots working alongside human operators will enhance efficiency and safety, especially in tasks that are repetitive or require heavy lifting, further refining the human element within automated systems. These advancements signify a future where **Computer Numerical Control** is not just about automating individual machines but about creating intelligent, interconnected, and highly adaptable manufacturing ecosystems. The core **CNC meaning** – automated control by a computer – will remain, but its capabilities and integration will reach unprecedented levels.Conclusion: The Enduring Impact of CNC
From its humble beginnings as Numerical Control to its current sophisticated state, **Computer Numerical Control (CNC)** has undeniably revolutionized the manufacturing world. The **CNC meaning** transcends a mere acronym; it represents a paradigm shift towards precision, efficiency, and automation that has reshaped industries globally. We've explored how **CNC machining** works as a subtractive process, guided by intricate G-code, and the essential components that bring these digital instructions to life. The widespread application of CNC across diverse materials and sectors – from the aerospace giants to the intricate medical device manufacturers – underscores its unparalleled advantages in delivering accuracy, repeatability, and speed. While challenges like initial investment and the need for skilled programming exist, the ongoing evolution of CNC, driven by AI, robotics, and smart manufacturing principles, promises an even more integrated and intelligent future. The journey of understanding **CNC meaning** reveals a technology that is not just about cutting metal, but about crafting the future. It empowers engineers and designers to push the boundaries of what's possible, creating products with unprecedented complexity and quality. What are your thoughts on the impact of CNC in daily life? Have you ever encountered a product that you suspect was made with CNC machining? Share your insights in the comments below! If you found this guide helpful, consider sharing it with others who might benefit from understanding this foundational manufacturing technology, and explore our other articles on cutting-edge industrial processes. Back to TopRelated Resources:
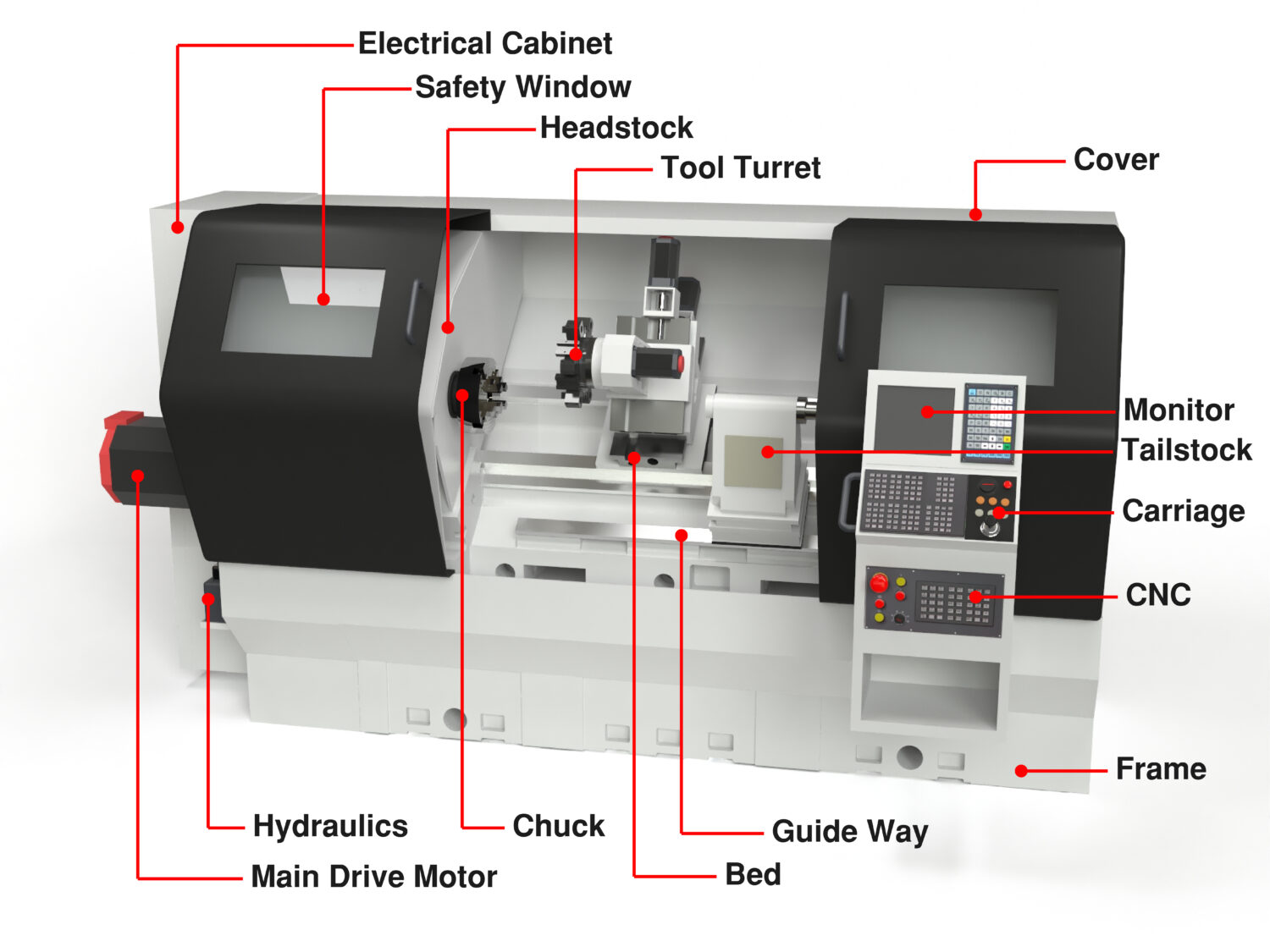
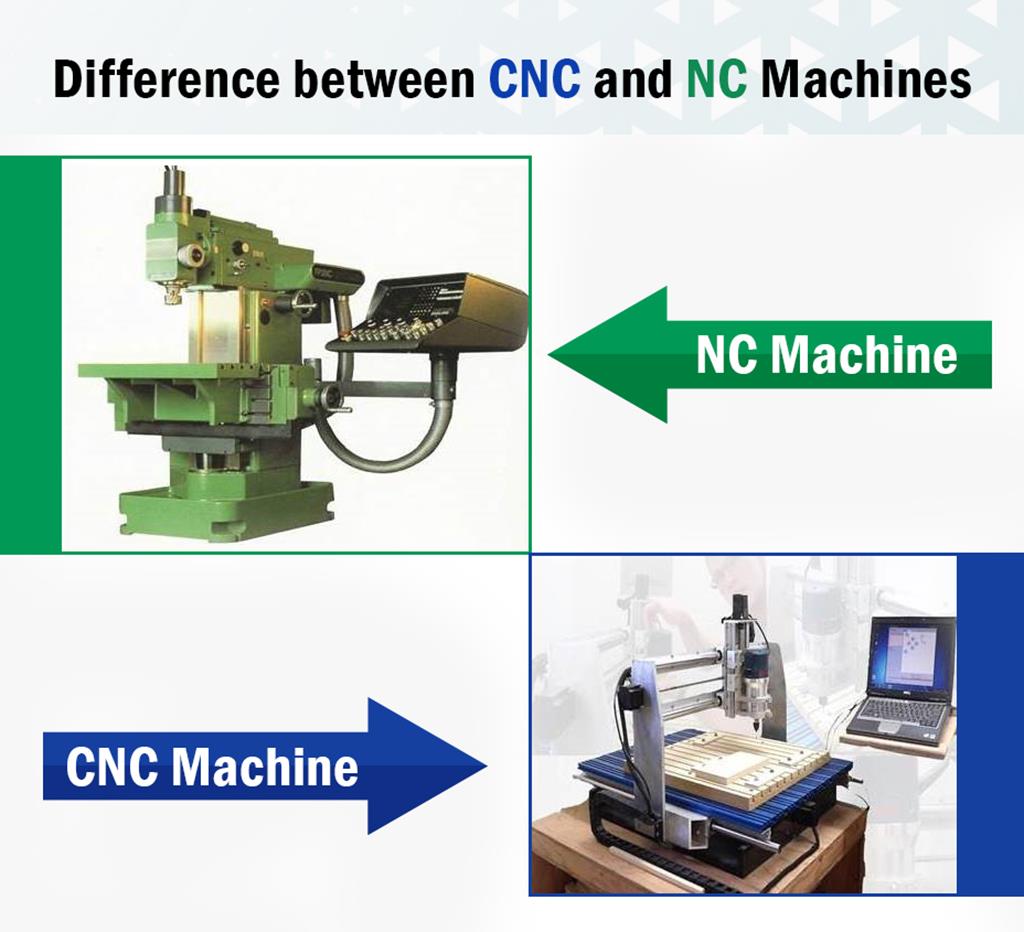

Detail Author:
- Name : Emanuel Douglas
- Username : yundt.urban
- Email : cbruen@hotmail.com
- Birthdate : 1986-03-29
- Address : 47525 Metz Isle Suite 075 Ashaland, IN 18383
- Phone : 1-262-464-9566
- Company : Homenick, Considine and Simonis
- Job : Fish Hatchery Manager
- Bio : Velit non ut quae possimus id laudantium id ipsa. Natus porro quis saepe iure. Omnis et corrupti expedita sequi.
Socials
linkedin:
- url : https://linkedin.com/in/amani_zieme
- username : amani_zieme
- bio : Possimus deserunt minima officiis explicabo.
- followers : 3107
- following : 1083
tiktok:
- url : https://tiktok.com/@amani.zieme
- username : amani.zieme
- bio : Eligendi omnis dolor corporis velit. Aut et odit aliquam porro.
- followers : 1625
- following : 2378
instagram:
- url : https://instagram.com/amani_official
- username : amani_official
- bio : Sed officia quaerat odit. Est tenetur qui possimus reiciendis. In iure sunt neque vitae.
- followers : 1510
- following : 2181
twitter:
- url : https://twitter.com/zieme2011
- username : zieme2011
- bio : Nihil praesentium nulla illo reiciendis. Itaque nisi esse blanditiis omnis accusantium. Maiores quis quaerat dolor ut.
- followers : 159
- following : 2657
facebook:
- url : https://facebook.com/amani8391
- username : amani8391
- bio : Eos inventore consequatur commodi.
- followers : 4474
- following : 1373