In the dynamic world of construction and infrastructure, innovation is the bedrock of progress. For decades, concrete has been the undisputed king, a testament to its strength and versatility. However, traditional concrete applications often come with inherent challenges: labor-intensive mixing, lengthy curing times, and significant logistical hurdles. Enter the "cement blanket," a groundbreaking material that's not just changing how we build, but fundamentally rethinking the very essence of rapid, robust, and adaptable construction. This remarkable invention is quickly becoming a game-changer, offering a compelling alternative to conventional methods for a myriad of applications, from erosion control to emergency infrastructure repair.
The cement blanket represents a significant leap forward, merging the foundational strength of cement with the flexibility and ease of a fabric. It’s a material that promises to streamline processes, reduce environmental impact, and provide durable solutions in scenarios where traditional concrete might be impractical or too time-consuming. As the global demand for efficient and sustainable building materials continues to rise, driven by factors like rapid urbanization, climate change mitigation, and the need for resilient infrastructure, understanding the capabilities and applications of this innovative material becomes paramount for anyone involved in the construction sector or simply curious about the future of building.
Table of Contents
- What Exactly is a Cement Blanket? Unpacking the Innovation
- The Transformative Advantages of Cement Blanket Technology
- Where Cement Blankets Shine: Diverse Applications Across Industries
- A Deep Dive into the Installation Process of Cement Blankets
- Cement Blankets vs. Traditional Concrete: A Comparative Analysis
- The Global Impact and Market Trends of Advanced Cement Solutions
- Choosing the Right Cement Blanket: Key Considerations for Your Project
- The Future of Construction: Innovations Beyond the Cement Blanket
What Exactly is a Cement Blanket? Unpacking the Innovation
At its core, a cement blanket, often referred to as Concrete Canvas™ (a prominent brand name), is a flexible, concrete-impregnated fabric that hardens on hydration to form a thin, durable, waterproof, and fire-resistant concrete layer. Imagine a roll of thick, robust fabric, but instead of just fibers, it's packed with a specially formulated dry cement mix. This innovative material is typically composed of a three-dimensional fiber matrix, which acts as a reinforcement, with a dry concrete powder blend embedded within it. The top surface is often coated with a PVC layer to ensure waterproofing, while the underside is usually a permeable non-woven fabric, allowing water to penetrate and initiate the hydration process.
The magic happens when the cement blanket comes into contact with water. Whether sprayed, immersed, or simply exposed to rain, the dry cement within the fabric rapidly absorbs the water, initiating a chemical reaction known as hydration. This process causes the cement to cure and harden, transforming the flexible fabric into a rigid, monolithic concrete structure. What sets this material apart is its ability to maintain its flexibility until hydration, allowing it to be draped over complex terrains, cut to size, and installed with remarkable ease. Once cured, it achieves impressive compressive strength, rivalling that of traditional poured concrete, but without the need for heavy machinery, mixing plants, or extensive formwork. This unique combination of properties makes the cement blanket an incredibly versatile and powerful tool in the modern construction arsenal, capable of delivering robust solutions with unprecedented speed and efficiency.
The Transformative Advantages of Cement Blanket Technology
The adoption of cement blanket technology is driven by a compelling suite of advantages that address many of the pain points associated with conventional concrete methods. These benefits extend beyond mere convenience, offering significant improvements in efficiency, cost-effectiveness, and environmental responsibility.
- Speed of Application: One of the most striking benefits is the dramatically reduced installation time. A team of just a few workers can deploy hundreds of square meters of cement blanket in a single day, a feat that would require significantly more labor and time with traditional concrete pouring. This rapid deployment capability is crucial for emergency repairs, time-sensitive projects, and large-scale infrastructure developments.
- Reduced Labor and Equipment: Because the material comes pre-mixed and ready for hydration, there's no need for concrete mixers, pumps, or extensive formwork. This translates directly into lower labor costs and a reduced reliance on heavy machinery, simplifying logistics and reducing the overall project footprint.
- Environmental Benefits: The cement blanket offers several environmental advantages. Its compact form reduces transport volume, leading to fewer vehicle emissions. Less waste is generated on-site compared to traditional concrete, which often involves excess material or formwork disposal. Furthermore, in certain applications, its use can prevent soil erosion, protecting natural habitats and water quality. While cement production itself is energy-intensive, innovations in application methods like the cement blanket contribute to a more efficient use of resources.
- Durability and Longevity: Once cured, the cement blanket forms a high-strength, durable concrete layer that is resistant to abrasion, chemicals, UV degradation, and fire. It offers excellent protection against erosion and weathering, ensuring a long service life for the installed structure. Its monolithic nature, without joints, also reduces potential weak points.
- Versatility and Adaptability: The flexibility of the cement blanket before hydration allows it to conform to irregular surfaces, complex geometries, and steep slopes that would be challenging or impossible for poured concrete. It can be cut with standard hand tools, making it highly adaptable to specific site requirements. This adaptability opens up a vast array of applications across various industries.
Where Cement Blankets Shine: Diverse Applications Across Industries
The unique properties of the cement blanket make it an ideal solution for a broad spectrum of applications, transcending traditional construction boundaries. Its ability to provide rapid, durable, and adaptable concrete solutions has seen it adopted in sectors ranging from civil engineering to disaster relief.
- Bourbon And Beyond 2025
- Hyatt Regency Mission Bay
- Fj Cruiser For Sale
- Bdn Bangor Maine
- Plymouth Grand 15
Erosion Control and Slope Stabilization
This is perhaps one of the most prominent applications for the cement blanket. Its ability to conform to undulating terrain and harden into a robust, erosion-resistant layer makes it perfect for lining drainage ditches, protecting riverbanks, stabilizing steep slopes, and preventing soil washout around critical infrastructure. Unlike traditional riprap or shotcrete, it provides a continuous, impermeable barrier that prevents water ingress and subsequent erosion, while being much faster and less disruptive to install. This application is particularly relevant in areas prone to heavy rainfall or water flow, where maintaining soil integrity is paramount.
Infrastructure Protection
The cement blanket offers an excellent solution for protecting existing infrastructure. It can be used as a protective lining for culverts, pipe protection, and bridge abutments, shielding them from environmental degradation, abrasion, and chemical attack. Its rapid deployment means minimal disruption to traffic or operations, making it ideal for maintenance and upgrade projects on active infrastructure. For instance, lining an aging culvert with a cement blanket can extend its lifespan significantly without the need for extensive excavation and replacement, saving both time and considerable financial outlay.
Rapid Road Repair and Pothole Solutions
In emergency situations or for quick fixes, the cement blanket can be deployed for rapid road repair, patching potholes, or even creating temporary access roads. Its quick setting time means that damaged areas can be made trafficable again within hours, minimizing disruption and improving safety. This capability is particularly valuable for disaster response teams or in remote locations where traditional concrete supplies and equipment are not readily available. The ease of transport and storage of rolls of cement blanket makes it an ideal material for such urgent needs.
Agricultural and Landscaping Uses
Beyond heavy civil applications, the cement blanket finds practical uses in agriculture and landscaping. It can be used to line irrigation ditches, create durable pond liners, or even suppress weed growth in specific areas. Its flexibility allows for creative landscaping features that require a robust, waterproof base, while its ease of installation makes it accessible for smaller-scale projects that might not justify the cost and complexity of poured concrete.
Military and Emergency Response
The deployable nature of the cement blanket makes it invaluable for military operations and emergency response scenarios. It can be used to rapidly construct temporary shelters, create landing pads, reinforce defensive positions, or establish quick access roads in challenging terrains. Its compact storage and rapid hardening capabilities mean that essential infrastructure can be established quickly and efficiently in remote or hostile environments, providing critical support when time is of the essence.
A Deep Dive into the Installation Process of Cement Blankets
One of the most compelling aspects of the cement blanket is its straightforward installation process, which significantly reduces the complexity and time typically associated with concrete work. While specific instructions may vary slightly by manufacturer, the general steps remain consistent, emphasizing ease of use and efficiency.
- Site Preparation: As with any construction project, proper site preparation is crucial. This involves clearing the area of debris, ensuring the ground is relatively smooth and free of sharp objects that could puncture the blanket. For erosion control, grading the slope to the desired profile is necessary. In some cases, a geotextile fabric might be laid underneath for additional stability or separation from the subgrade.
- Laying the Blanket: Rolls of cement blanket are typically unrolled and positioned over the prepared surface. The material is flexible enough to be draped over contours, around obstacles, and down slopes. Sections can be overlapped (typically by 100mm) and secured using various methods such as staples, screws, or specialized clips, depending on the application and substrate. The ease with which the material can be cut with standard utility knives allows for precise fitting around structures or for creating specific shapes.
- Hydration Methods: This is where the transformation occurs. The dry cement within the blanket needs to be saturated with water.
- Spraying: For most applications, water is simply sprayed onto the blanket using a hose or a sprayer. It's important to ensure even saturation across the entire surface. The material is designed to absorb the water quickly and efficiently.
- Immersion: For smaller pieces or specific applications like lining a ditch, the blanket can be pre-cut and immersed in water before being laid into place. This method ensures complete saturation.
- Natural Rainfall: In some long-term, non-critical applications, the blanket can even be laid out and allowed to hydrate naturally with rainfall, though controlled hydration is always recommended for optimal performance.
- Curing: Once hydrated, the cement blanket begins to cure. The initial set typically occurs within a few hours, and the material becomes walkable within 24 hours. Full strength is usually achieved within 24-48 hours, though this can vary based on temperature and humidity. Unlike traditional concrete, no special curing compounds or extensive covering are typically needed, as the PVC backing often helps retain moisture for proper hydration.
- Safety Considerations: While installation is simpler, standard construction safety practices should still be observed. This includes wearing appropriate personal protective equipment (PPE) such as gloves and eye protection, especially during cutting and hydration.
The simplicity of this process, combined with the material's inherent properties, drastically reduces project timelines and labor requirements, making the cement blanket an incredibly efficient solution for a wide array of construction challenges.
Cement Blankets vs. Traditional Concrete: A Comparative Analysis
While both cement blankets and traditional poured concrete rely on the same fundamental chemical reaction (hydration of cement) to achieve strength, their application methods, performance characteristics, and overall project implications differ significantly. Understanding these distinctions is key to selecting the optimal material for a given project.
- Cost-Effectiveness:
- Traditional Concrete: The upfront material cost of bulk cement and aggregates might seem lower. However, when you factor in the cost of labor for mixing, pouring, finishing, formwork, heavy machinery rental (mixers, pumps), and disposal of waste, the overall project cost can escalate significantly, especially for smaller or remote projects.
- Cement Blanket: The material itself often has a higher per-unit cost than raw concrete materials. However, its major cost savings come from drastically reduced labor, elimination of heavy equipment, minimal site preparation, and faster project completion. For many applications, particularly those involving difficult access, steep slopes, or urgent repairs, the total installed cost of a cement blanket can be considerably lower than traditional concrete.
- Performance in Specific Scenarios:
- Traditional Concrete: Excellent for large-scale structural foundations, high-load bearing applications, and flat, accessible surfaces where uniform thickness and high compressive strength are paramount. It requires careful control of slump and curing conditions.
- Cement Blanket: Excels in applications requiring rapid deployment, conformity to irregular surfaces, erosion control, and situations where access is limited. While it achieves high compressive strength, it's typically used for non-structural lining, protection, and stabilization rather than primary load-bearing structures. Its continuous, jointless surface is superior for waterproofing and preventing water ingress compared to segmented poured concrete.
- Environmental Impact:
- Traditional Concrete: The production of Portland cement is energy-intensive and a significant contributor to global CO2 emissions. On-site mixing can lead to material waste, water runoff, and dust.
- Cement Blanket: While still containing cement, the reduced transportation volume (no water or aggregates until deployment), minimal on-site waste, and elimination of heavy machinery can lead to a smaller overall carbon footprint for specific applications. Its ability to prevent erosion also has positive environmental impacts on soil and water quality.
- Ease of Transport and Storage:
- Traditional Concrete: Requires bulk transport of cement, aggregates, and water, often necessitating large trucks and storage silos on site.
- Cement Blanket: Comes in compact rolls, making it easy to transport to remote locations, carry by hand, and store efficiently. This logistical advantage is a major benefit for projects with challenging access or limited space.
In essence, the cement blanket isn't designed to replace traditional concrete entirely, but rather to complement it by offering a highly efficient, specialized solution for specific challenges where conventional methods are impractical, too slow, or excessively costly. It represents an evolution in material science, providing targeted benefits for a modern construction landscape.
The Global Impact and Market Trends of Advanced Cement Solutions
The advent of materials like the cement blanket is a testament to the ongoing innovation within the broader cement and construction industries. This sector, as highlighted by "The Cement Plant Operations Handbook Seventh Edition," which serves as a standard reference for manufacturing, is constantly evolving, driven by global demand, economic shifts, and a push for more sustainable and efficient practices. The demand for cement and its derivatives remains robust, albeit with regional fluctuations and challenges.
Consider the recent market dynamics: "Cement sales in Indonesia amounted to 5.314mt in May, a drop of 3.8 per cent yoy compared to the 5.527mt reported a year earlier, according to the Asosiasi Semen Indonesia." Such declines can be attributed to various factors, including economic slowdowns or shifts in construction project pipelines. Conversely, "Cement dispatches in Vietnam increased by 17 per cent yoy to 7.086mt in May 2025, according to the Vietnam National Cement Association (VNCA)," indicating strong growth in that region, likely fueled by infrastructure development and urbanization. These contrasting trends underscore the diverse global landscape of cement consumption and the need for adaptable solutions.
The global cement industry is also navigating complex trade policies. For instance, "Canadian and Greek cement producers will be hit hardest by US tariffs, adding to the already announced 25 per cent tariff on Canadian and Mexican imports, on 2 April the US." Such tariffs can reshape supply chains, influencing the cost and availability of traditional cement and, by extension, advanced materials like the cement blanket that rely on cement as a core component. Companies like Cement Australia, which "operates in cement, concrete, quarry products, asphalt and transport, strengthening Cement Australia's portfolio," are diversifying their offerings to maintain market resilience amidst these changes, potentially incorporating innovative products to meet evolving demands.
The push for specialized products is also evident in new production facilities. "The first kiln firing took place on 1 October 2022," for CPCMC, which "will produce cement under the PRO (blended hydraulic cement) and PRIME (OPC) brands." This focus on blended and Ordinary Portland Cement (OPC) brands reflects the industry's commitment to meeting diverse market needs, including the base materials for advanced composites. "Most of Bangladesh’s cement exports are destined for India, particularly the northeastern states, Other notable destinations include Nepal, Sri Lanka, and the Maldives," illustrating regional trade dynamics that can influence the adoption of new materials. Staying informed on these trends is vital, and resources like "International Cement Review Magazine" provide invaluable "cement industry news and updates" for professionals tracking these developments.
The global market for advanced cement solutions, including the cement blanket, is expected to grow as countries prioritize rapid infrastructure development, disaster preparedness, and sustainable construction practices. The ability of these materials to offer quick, efficient, and durable solutions positions them favorably in a world increasingly demanding smarter ways to build and protect.
Choosing the Right Cement Blanket: Key Considerations for Your Project
While the cement blanket offers impressive versatility, selecting the appropriate type and ensuring its suitability for your specific project is crucial for optimal performance and longevity. Not all cement blankets are created equal, and careful consideration of several factors will guide your decision.
- Thickness and Strength Requirements: Cement blankets are available in various thicknesses, which directly correlate to their final compressive strength and durability. Thicker blankets offer greater structural integrity and abrasion resistance. Assess the specific demands of your application: Is it for light erosion control, or does it need to withstand significant water flow or impact? Consult manufacturer specifications for strength ratings and choose a thickness that exceeds your minimum requirements for safety and longevity.
- Environmental Conditions: Consider the environment where the cement blanket will be deployed. Will it be exposed to extreme temperatures, harsh chemicals, or continuous UV radiation? While most cement blankets are designed for robust outdoor performance, some formulations may offer enhanced resistance to specific environmental stressors. Ensure the product chosen is rated for the expected conditions to prevent premature degradation.
- Project Scale and Accessibility: For very large projects, consider the logistics of transporting and deploying large rolls. For smaller, intricate jobs or areas with difficult access, the ease of cutting and manipulating the material by hand becomes a significant advantage. Evaluate whether the project warrants the use of specialized installation equipment (though often minimal) or if manual deployment is feasible and efficient.
- Supplier Reputation and Technical Support: Choose a reputable manufacturer or supplier known for quality products and reliable technical support. Inquire about product certifications, testing data, and case studies. A good supplier can offer valuable guidance on installation best practices, troubleshoot potential issues, and provide detailed product specifications, ensuring you maximize the benefits of the cement blanket for your specific application.
- Cost-Benefit Analysis: While we've discussed the overall cost-effectiveness, it's important to conduct a detailed cost-benefit analysis for your project. Compare the total installed cost of the cement blanket (material + minimal labor) against traditional methods (materials + extensive labor + equipment + disposal). Factor in the value of rapid deployment, reduced disruption, and long-term durability. Often, the higher material cost of the cement blanket is quickly offset by savings in labor, time, and associated project complexities.
By carefully evaluating these considerations, you can make an informed decision that ensures the cement blanket performs as expected, delivering a durable and efficient solution tailored to your project's unique needs.
The Future of Construction: Innovations Beyond the Cement Blanket
The cement blanket is more than just a product; it's a symbol of the evolving construction industry's commitment to innovation, efficiency, and sustainability. As we look ahead, the trajectory of construction materials and methodologies points towards even more advanced solutions, building on the principles exemplified by the cement blanket.
Expect to see continued research and development in areas such as self-healing concrete, which can automatically repair cracks, extending the lifespan of structures and reducing maintenance costs. Smart concretes, embedded with sensors, will provide real-time data on structural integrity, temperature, and moisture levels, allowing for predictive maintenance and enhanced safety. Furthermore, the drive for greener construction will intensify, leading to the widespread adoption of low-carbon cements, recycled aggregates, and bio-based binders, significantly reducing the environmental footprint of building materials. The integration of robotics and automation in construction, from 3D printing of entire buildings to automated material placement, will further streamline processes and enhance precision. The future of construction is not just about building bigger or faster, but about building smarter, more sustainably, and with an adaptability that can meet the complex challenges of a rapidly changing world. The cement blanket is a crucial step on this exciting journey, paving the way for a new era of resilient and innovative infrastructure.
The cement blanket stands as a testament to human ingenuity, transforming a centuries-old material into a flexible, rapidly deployable solution for modern challenges. Its ability to simplify complex construction tasks, reduce environmental impact, and provide robust, long-lasting results makes it an indispensable tool for engineers, contractors, and anyone invested in the future of building. From preventing erosion along vital waterways to providing immediate relief in disaster zones, the applications of this innovative material are as diverse as they are impactful. As the construction industry continues its quest for efficiency and sustainability, the cement blanket will undoubtedly remain at the forefront, inspiring further advancements that promise to reshape our built environment for the better.
Have you had experience with cement blankets in your projects, or do you see other potential applications for this fascinating material? Share your thoughts and insights in the comments below, or consider sharing this article to spark a wider conversation about the future of construction materials!
Related Resources:
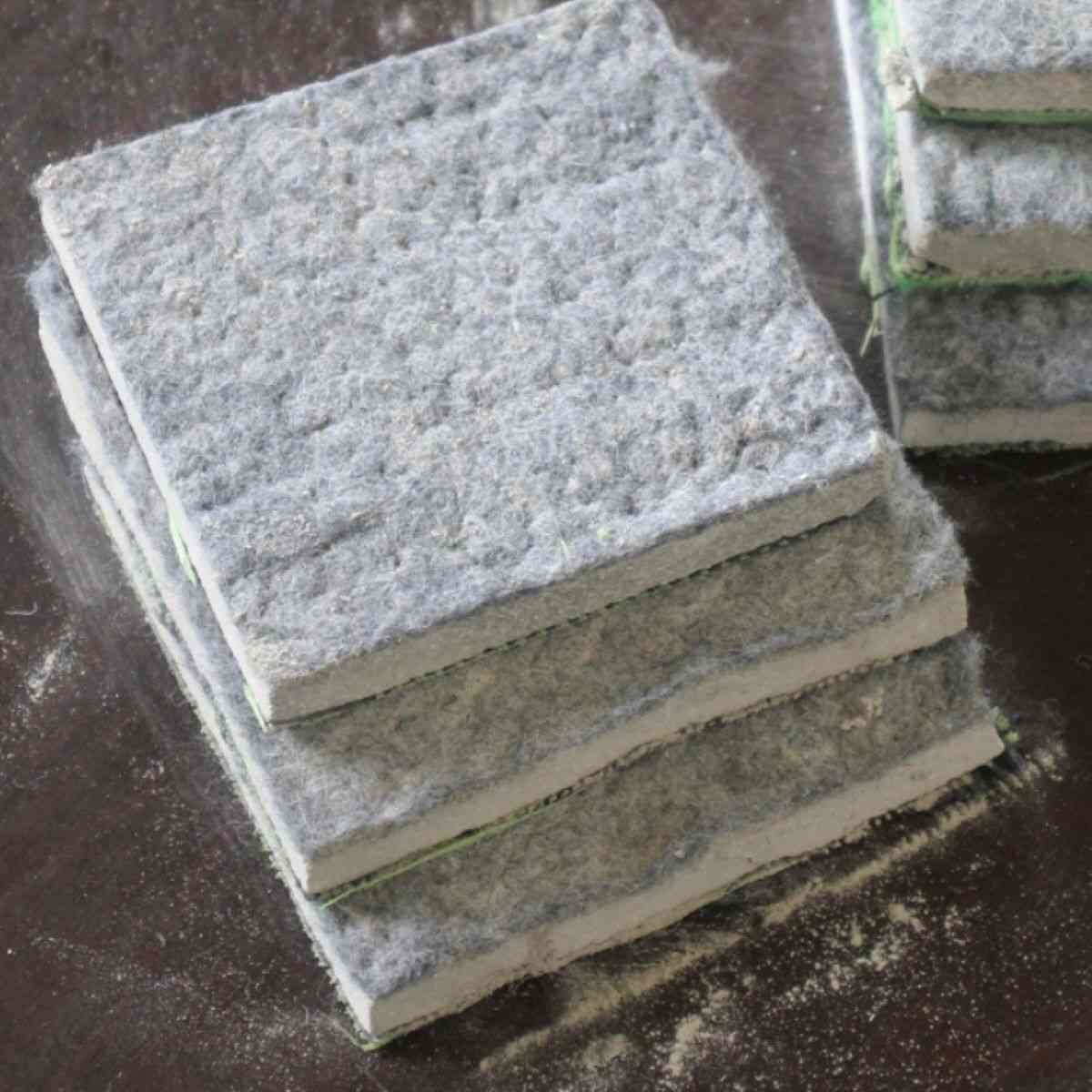
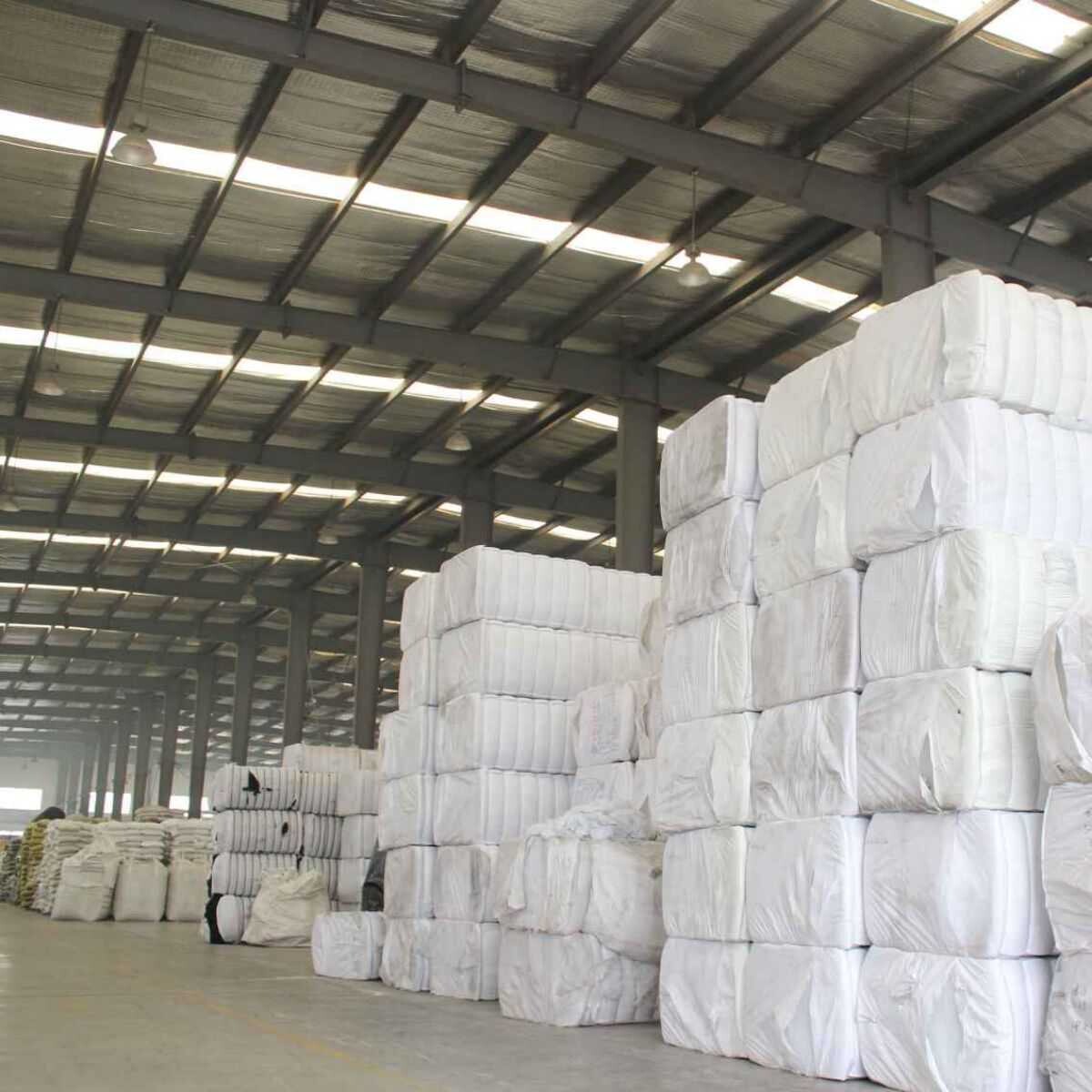
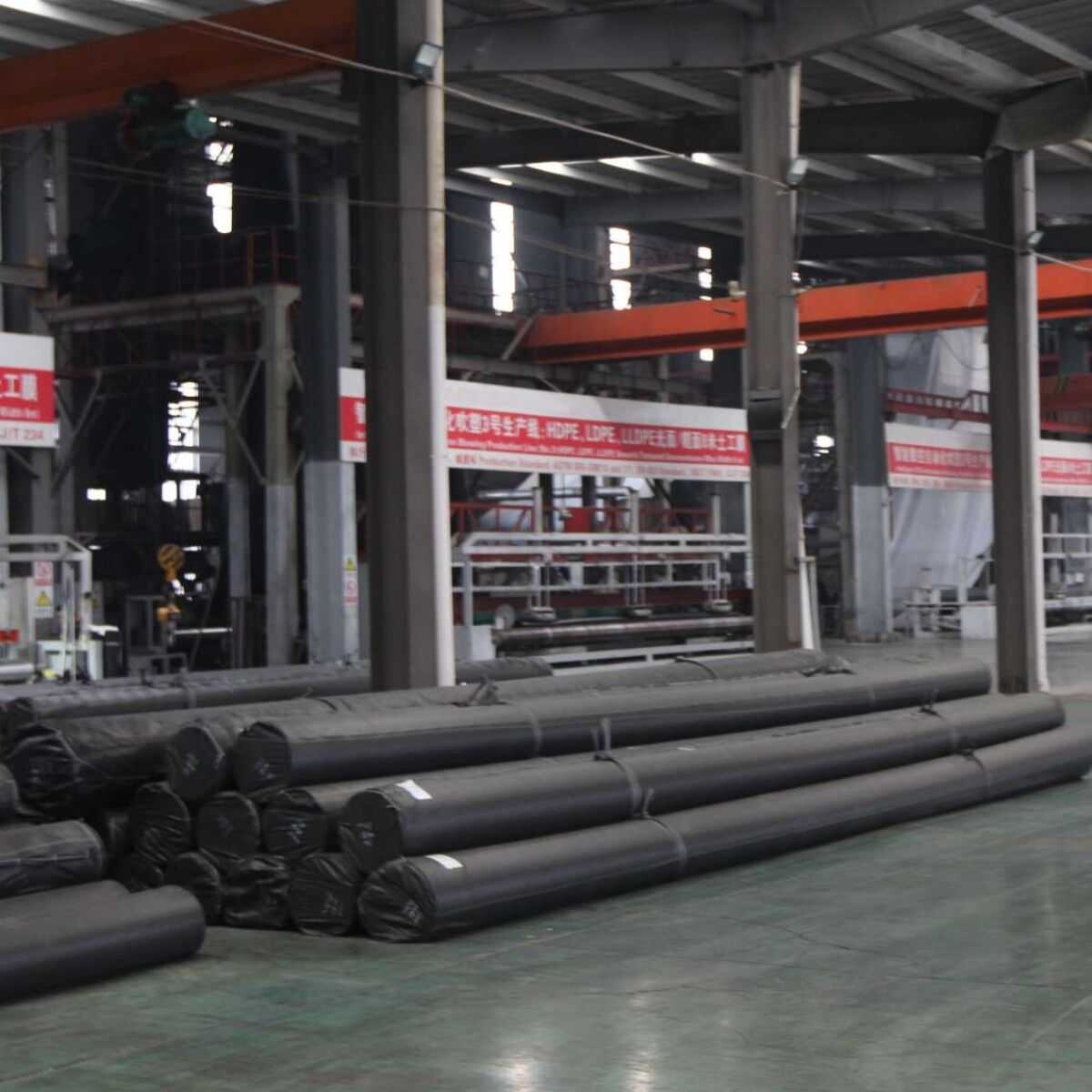
Detail Author:
- Name : Davonte Barrows
- Username : baylee52
- Email : jailyn39@cole.com
- Birthdate : 1998-04-11
- Address : 104 Tillman Ford Suite 155 Kristamouth, KY 55659
- Phone : 956-232-4349
- Company : Zemlak, Erdman and McDermott
- Job : Chemistry Teacher
- Bio : Eius sapiente omnis sed. Dolorem ipsum eum aut quae. Excepturi ducimus fugiat amet.
Socials
linkedin:
- url : https://linkedin.com/in/jankunding
- username : jankunding
- bio : Quisquam aliquam velit ratione.
- followers : 6975
- following : 1403
facebook:
- url : https://facebook.com/julia1022
- username : julia1022
- bio : Rem repudiandae molestias expedita ipsa totam.
- followers : 2503
- following : 1708