**For any business or individual relying on a steady, clean supply of ice, the Manitowoc ice machine stands as a cornerstone of daily operations. Renowned for their durability and efficiency, these machines are a significant investment, and understanding their intricacies is paramount to ensuring their longevity and consistent output. From the bustling kitchens of restaurants to the quiet corridors of healthcare facilities, a well-maintained Manitowoc ice machine is not just a convenience; it's a necessity, directly impacting customer satisfaction and operational efficiency.** This comprehensive guide delves into the world of Manitowoc ice makers, offering practical insights, maintenance tips, and troubleshooting advice drawn from years of collective experience, ensuring your unit operates at its very best. Maintaining a Manitowoc ice machine isn't merely about fixing problems when they arise; it's about proactive care that prevents costly breakdowns and ensures the quality of your ice. We'll explore everything from routine cleaning protocols and understanding key components to advanced troubleshooting for common issues like harvest cycle anomalies and control board replacements. Our aim is to empower you with the knowledge to keep your Manitowoc machine running smoothly, highlighting when a simple reset will suffice and when it's time to call in the certified professionals.
Table of Contents
- The Unsung Hero: Understanding Your Manitowoc Ice Machine
- Essential Maintenance for Optimal Performance of Your Manitowoc Ice Machine
- Troubleshooting Common Issues with Your Manitowoc Ice Machine
- Advanced Repairs: When to Call the Experts for Your Manitowoc Ice Machine
- Maximizing the Lifespan of Your Manitowoc Ice Machine: Pro Tips
- Why Manitowoc Ice Machines are a Smart Investment
- Frequently Asked Questions About Manitowoc Ice Machines
- Your Insights Matter: Join the Manitowoc Ice Machine Community
The Unsung Hero: Understanding Your Manitowoc Ice Machine
Manitowoc ice machines have long been a gold standard in the commercial ice production industry. Their reputation for reliability, efficiency, and innovative design precedes them, making them a preferred choice for a diverse range of environments, from bustling restaurants and hotels to hospitals and educational institutions. These machines are engineered to produce a consistent supply of high-quality ice, which is crucial for operations where ice is not just a luxury but a fundamental requirement. Whether it’s the crystal-clear cubes for beverages, the flaked ice for food preservation, or the nugget ice for specialty drinks, Manitowoc offers a model tailored to specific needs. Understanding your specific Manitowoc ice machine model, be it a Neo, Indigo, or another series, is the first step towards effective maintenance and troubleshooting. Each series boasts unique features and technologies designed to optimize ice production and energy efficiency. For instance, the Indigo series is renowned for its intelligent diagnostics and easy-to-use control panels, while the Neo series offers compact designs ideal for smaller spaces without compromising on output. Familiarity with your unit's specific characteristics, as detailed in its user manual or the Manitowoc Neo technician handbook, will empower you to identify issues more quickly and perform routine maintenance with confidence. This foundational knowledge is key to unlocking the full potential and extending the operational life of your valuable Manitowoc ice machine.Essential Maintenance for Optimal Performance of Your Manitowoc Ice Machine
Regular and thorough maintenance is not just a recommendation; it's a critical requirement for any Manitowoc ice machine. Neglecting routine care can lead to a host of problems, from diminished ice production and poor ice quality to complete machine failure and costly repairs. Proactive maintenance ensures your machine runs efficiently, produces clean, safe ice, and extends its overall lifespan, protecting your investment.The Critical Role of Regular Cleaning
One of the most vital aspects of Manitowoc ice machine maintenance is consistent cleaning. The general consensus among experienced technicians and the manufacturer’s guidelines is that a thorough cleaning should be performed when ice production begins to dwindle, which often occurs approximately every six months. This semi-annual cleaning schedule helps prevent mineral buildup, mold, and mildew, all of which can significantly impair performance and compromise ice quality. If the machine is exceptionally dirty, a standard cleaning might not suffice. In such cases, it’s advisable to take the unit apart for deep cleaning. This allows access to components that might otherwise be difficult to reach, ensuring all parts are free from contaminants. It’s absolutely crucial to note that only Manitowoc ice machine cleaner and sanitizer are approved for use in Manitowoc ice makers. Using unapproved chemicals can damage the machine's components, void warranties, and potentially leave harmful residues in your ice. Always follow the manufacturer’s instructions meticulously for cleaning and sanitizing, ensuring proper dilution and contact times. Remember, safety first: always disconnect power to the ice machine before beginning any cleaning procedure.Understanding Key Components and Their Maintenance
A Manitowoc ice machine is a complex system of interconnected parts, each playing a vital role in the ice-making process. Understanding these components and their common issues can greatly assist in troubleshooting and preventative maintenance. One fundamental component is the water pump. This essential part of a Manitowoc ice machine is responsible for pumping water from the water trough to the distribution tube, from where it subsequently flows over the evaporator plate to form ice. If the water pump is malfunctioning, water won't properly circulate, leading to poor ice formation or no ice production at all. Regular checks for blockages or signs of wear on the pump can prevent significant downtime. Another component that is a frequent offender when it comes to operational issues is the water curtain. This curtain, which opens and closes during the harvest cycle to release ice, can become stiff, cracked, or misaligned over time. Issues with the water curtain can prevent ice from dropping properly into the bin or cause the machine to get stuck in the harvest cycle. While servicing Manitowoc ice machines for over a decade, many technicians have observed that the water curtain is a much more common source of problems than other components like the bin switch. In fact, in short dozen years servicing Manitowoc ice machines, it's rare to ever have to replace a bin switch, highlighting its robust design. However, the water curtain often requires attention due to its constant movement and exposure to water. Regular inspection of the water curtain for flexibility and proper movement can preempt many harvest cycle issues.Troubleshooting Common Issues with Your Manitowoc Ice Machine
Even with diligent maintenance, a Manitowoc ice machine can occasionally encounter operational hiccups. Knowing how to diagnose and address common problems can save time and money, allowing you to resolve minor issues quickly or provide accurate information to a service technician.Resetting Neo and Indigo Models
One of the simplest yet most effective troubleshooting steps for many electronic devices, including Manitowoc ice machines, is a system reset. For more training tips on Manitowoc ice machines, learning how to reset both the Neo and Indigo models is a fundamental skill. A reset can often clear minor software glitches or sensor errors that might be causing irregular operation. Specifically, for the Manitowoc Neo series, the technician handbook states that if switches aren't working properly on the Neo touch pad, a reset and test will need to be performed. This involves a specific sequence of actions to cycle the machine's power and internal diagnostics. Always ensure you disconnect power to the ice machine to safely initiate any reset procedure. This power cycle, often referred to as a "hard reset," can resolve temporary communication errors between the control board and the touchpad, restoring normal functionality. While a reset is a good first step, persistent issues with the touchpad or other controls may indicate a more serious underlying problem that requires professional attention.Addressing Harvest Cycle Anomalies
The harvest cycle is a critical phase where the ice slab is released from the evaporator and drops into the ice bin. Issues during this cycle are among the most common complaints for Manitowoc ice machine owners. For instance, with a Manitowoc Indigo NXT 450 (ID0452A), random issues during the harvest cycle are not uncommon. The machine will go into harvest cycle like it's supposed to, but most of the time the curtain will stay, preventing the ice from dropping or causing the machine to get stuck. This can lead to reduced ice production or even a complete shutdown if the machine's safety protocols are triggered. As mentioned earlier, the water curtain is a frequent offender in these scenarios. If the curtain is sticking, not fully opening, or not returning to its closed position, it will disrupt the harvest process. This could be due to mineral buildup, physical damage, or a problem with the motor or sensor that controls the curtain's movement. Troubleshooting harvest cycle issues often involves inspecting the water curtain for obstructions or damage, ensuring it moves freely. If the curtain is staying put when it should be opening, or vice versa, it's a strong indicator of a problem that needs immediate attention. Sometimes, a thorough cleaning of the curtain and its pivot points can resolve the issue, but persistent problems may require component replacement.Advanced Repairs: When to Call the Experts for Your Manitowoc Ice Machine
While routine maintenance and basic troubleshooting can be performed by diligent owners, certain repairs on a Manitowoc ice machine require the expertise of trained, certified technicians. Attempting complex repairs without proper knowledge or tools can lead to further damage, void warranties, and pose safety risks. One such advanced repair involves the control board. Learning how to replace and set up a new control board in a Manitowoc Ice Indigo ice machine unit is a task specifically outlined in guides for authorized service technicians. The control board is the "brain" of the ice machine, managing all its functions, from water fill and ice production to harvest cycles and diagnostic codes. A malfunctioning control board can manifest in a variety of symptoms, including erratic behavior, non-responsiveness, or incorrect error codes. Replacing it requires not only technical skill but also access to specific diagnostic tools and programming knowledge to ensure the new board is correctly configured for the specific model. Similarly, the initial installation of a Manitowoc Indigo series ice machine, ice bin, and other related components is a task that must be handled by trained, certified technicians. This thorough guide for installation ensures that the unit is properly leveled, connected to water and power supplies, and correctly plumbed for drainage, all critical steps for optimal performance and to prevent future issues. Incorrect installation can lead to water leaks, inefficient operation, or even safety hazards. For any issue that goes beyond basic cleaning or simple resets, or involves electrical components, refrigerants, or complex mechanical parts, it is always best to disconnect power to the ice machine and contact a qualified Manitowoc service professional. Their expertise ensures that repairs are done correctly, safely, and in accordance with manufacturer specifications, preserving the integrity and performance of your valuable Manitowoc ice machine.Maximizing the Lifespan of Your Manitowoc Ice Machine: Pro Tips
Extending the life of your Manitowoc ice machine beyond its expected years requires more than just reactive repairs; it demands a proactive approach to care and operation. Here are some professional tips to help you maximize your unit's lifespan and ensure consistent, high-quality ice production. Firstly, adhere strictly to the recommended cleaning schedule. As previously mentioned, a thorough cleaning every six months, or whenever ice production begins to dwindle, is non-negotiable. This prevents mineral scale buildup, which is a primary culprit for reduced efficiency and component wear. Always use only Manitowoc ice machine cleaner and sanitizer, as these products are specifically formulated to be effective without damaging the machine's internal components. Secondly, pay attention to the environment where your machine operates. Extreme temperatures, poor ventilation, or excessive dust can all negatively impact performance and longevity. Ensure your ice machine has adequate airflow around it, and keep the area clean to prevent dust and debris from entering the system. Regularly clean the condenser coils, as dirty coils force the machine to work harder, leading to increased energy consumption and premature wear on the compressor. Thirdly, consider the quality of your water supply. Hard water, rich in minerals, is the leading cause of scale buildup. Installing a high-quality water filter system specifically designed for ice machines can significantly reduce mineral deposits, thereby extending the life of components like the evaporator plate, water pump, and distribution tube. Filters should be replaced according to the manufacturer's recommendations, typically every 3-6 months depending on water quality and usage. Finally, establish a routine for professional inspections. While you can handle daily and weekly checks, an annual inspection by a certified Manitowoc technician can identify potential issues before they escalate into major problems. They can check refrigerant levels, electrical connections, and the overall mechanical integrity of the unit, providing insights and adjustments that prolong the life of your Manitowoc ice machine.Why Manitowoc Ice Machines are a Smart Investment
Investing in a Manitowoc ice machine is more than just purchasing equipment; it's a strategic decision for businesses and organizations that rely on consistent, high-quality ice. The initial cost might seem significant, but the long-term benefits and return on investment make Manitowoc machines a truly smart choice. Their reputation for durability is well-earned. Built with robust materials and engineered for demanding commercial environments, Manitowoc ice machines are designed to withstand continuous operation. This inherent reliability translates into less downtime for repairs and more consistent ice production, which is crucial for maintaining operational flow and customer satisfaction. A machine that consistently performs means fewer disruptions and a more predictable supply chain for your ice needs. Furthermore, Manitowoc machines are known for their energy efficiency. Modern models incorporate advanced technologies that minimize water and power consumption, leading to substantial savings on utility bills over the machine's lifespan. This focus on efficiency not only benefits your bottom line but also aligns with environmental sustainability goals, reducing your carbon footprint. The availability of parts and the extensive network of authorized service technicians also add to the value proposition. When issues do arise, access to genuine Manitowoc parts and skilled professionals ensures that repairs are done correctly and efficiently, minimizing the impact on your operations. This strong support system provides peace of mind, knowing that your investment is protected and that expert help is readily available. Ultimately, the combination of reliability, efficiency, and comprehensive support makes a Manitowoc ice machine a cost-effective solution in the long run. It's an investment that pays dividends through consistent performance, lower operating costs, and the assurance of a dependable ice supply, solidifying its position as a leader in the commercial ice machine market.Frequently Asked Questions About Manitowoc Ice Machines
Here are some common questions about Manitowoc ice machines, providing quick answers to help you better understand and maintain your unit. **Q: How often should I clean my Manitowoc ice machine?** A: A thorough cleaning is recommended every six months, or more frequently if you notice a decrease in ice production or a change in ice quality. If the machine is exceptionally dirty, a deep clean requiring disassembly may be necessary. **Q: Can I use any cleaner for my Manitowoc ice machine?** A: No. It is imperative that only Manitowoc ice machine cleaner and sanitizer are approved for use in Manitowoc ice makers. Using other chemicals can damage the machine and void its warranty. **Q: What should I do if my Manitowoc ice machine is not producing enough ice?** A: First, check if it's due for a cleaning, as mineral buildup can significantly reduce production. Ensure the water pump is functioning correctly and that the water curtain is moving freely during the harvest cycle. If issues persist, consider performing a reset (for Neo and Indigo models) or contact an authorized service technician. **Q: My Manitowoc ice machine's harvest cycle seems stuck. What's wrong?** A: This is a common issue, and the water curtain is a frequent offender. Check if the curtain is sticking, damaged, or obstructed. The machine will go in harvest cycle like it’s supposed to, but most of the time the curtain will stay, indicating a problem. **Q: When should I call a professional technician for my Manitowoc ice machine?** A: For complex issues like control board replacement in an Indigo unit, persistent harvest cycle problems after basic troubleshooting, or any issues involving electrical components or refrigerants, it's best to call a trained, certified Manitowoc service technician. Disconnect power to the ice machine before any professional service begins.Your Insights Matter: Join the Manitowoc Ice Machine Community
The collective wisdom of users and technicians is an invaluable resource. If you have any insight or experiences with maintaining Manitowoc models, especially unique troubleshooting tips, preventative measures you've found effective, or stories about overcoming challenging issues, we encourage you to share them. Your contributions can help others facing similar situations, fostering a community of informed Manitowoc ice machine owners and operators. Whether it's a specific trick for resetting a stubborn Neo touchpad, an observation about the longevity of certain components, or advice on deep cleaning techniques, your real-world experience is incredibly valuable. Leave your comments and insights below, and let's build a comprehensive knowledge base together for mastering the Manitowoc ice machine.Conclusion
The Manitowoc ice machine is a testament to robust engineering and consistent performance, a true workhorse in countless commercial settings. As we've explored, its longevity and efficiency are not solely dependent on its initial build quality but heavily on diligent maintenance and informed troubleshooting. From understanding the critical role of regular cleaning with approved Manitowoc ice machine cleaner and sanitizer to recognizing the signs of common component failures like issues with the water pump or the frequently offending water curtain, proactive care is paramount. We've also highlighted the importance of knowing when a simple reset for Neo and Indigo models can resolve a glitch, and when complex repairs, such as control board replacement or initial installation, necessitate the expertise of authorized, certified technicians. By adhering to these guidelines, prioritizing safety (always disconnect power to the ice machine before any work), and embracing a proactive approach to maintenance, you not only ensure a steady supply of high-quality ice but also protect your significant investment. Your Manitowoc ice machine is designed for durability, and with the right care, it will continue to serve your needs reliably for years to come. We encourage you to put these tips into practice and share your own experiences. For more training tips on Manitowoc ice machines, continue exploring our resources, and remember that a well-maintained machine is a cornerstone of a successful operation.Related Resources:
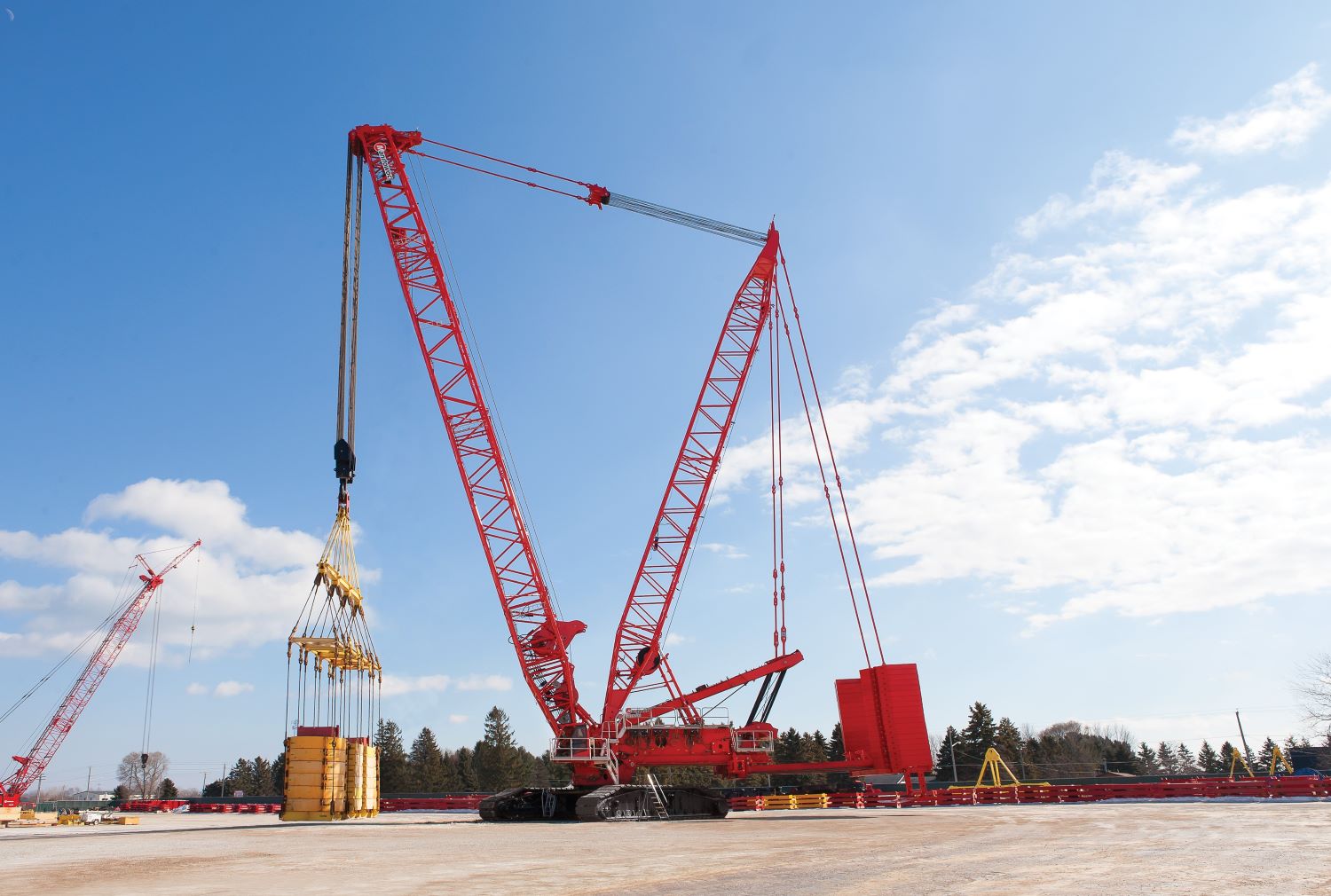
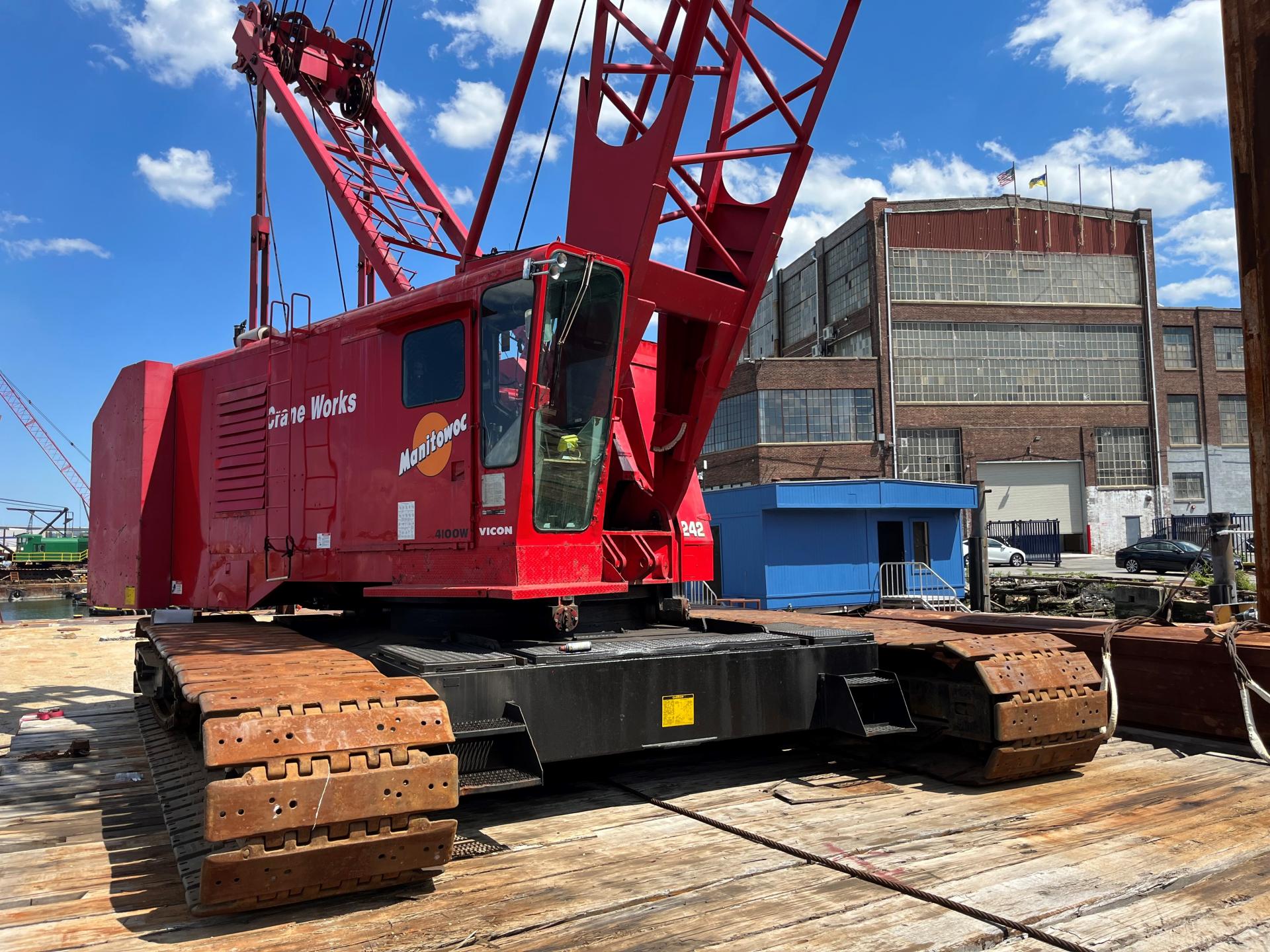
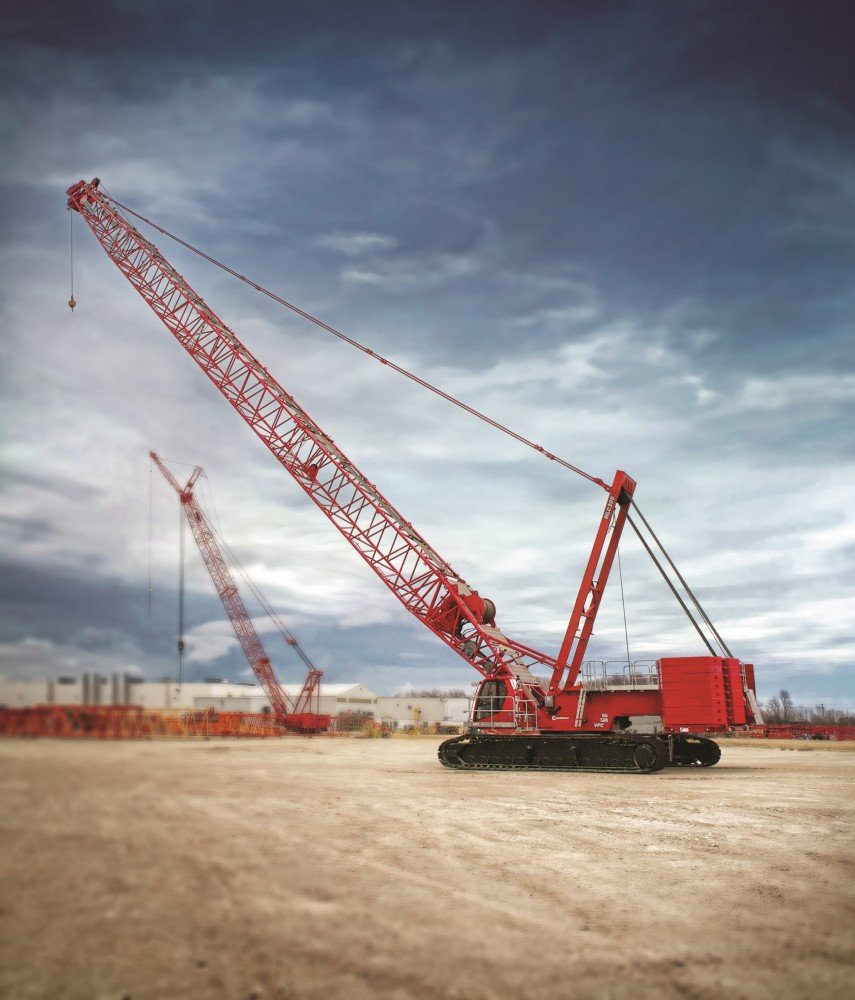
Detail Author:
- Name : Jameson Hane
- Username : mschmidt
- Email : uharber@hotmail.com
- Birthdate : 1988-09-20
- Address : 823 Maurine Brooks Cummeratafort, UT 92337
- Phone : (765) 763-7493
- Company : Lemke Inc
- Job : Signal Repairer OR Track Switch Repairer
- Bio : Iste dignissimos quia quod incidunt nam. Voluptatem omnis esse qui sed cupiditate voluptas ut maxime. Qui commodi laborum laboriosam iste corrupti repellendus. Fugiat quo nihil minus dolorem.
Socials
twitter:
- url : https://twitter.com/hmacejkovic
- username : hmacejkovic
- bio : Quibusdam est nihil nesciunt et. Eligendi quo sit adipisci aperiam. Officia in eum porro dolorum vitae ad soluta.
- followers : 4282
- following : 1692
tiktok:
- url : https://tiktok.com/@hettie.macejkovic
- username : hettie.macejkovic
- bio : Quia tempore vero corporis vel est dolorem.
- followers : 5646
- following : 1253
instagram:
- url : https://instagram.com/hettie_official
- username : hettie_official
- bio : Aut sit neque totam. Maiores amet corrupti odit iste aut iure soluta. Autem provident soluta qui.
- followers : 6417
- following : 1726
linkedin:
- url : https://linkedin.com/in/macejkovic2001
- username : macejkovic2001
- bio : Vel et quas quaerat quis.
- followers : 3646
- following : 1683
facebook:
- url : https://facebook.com/macejkovic2024
- username : macejkovic2024
- bio : Repellat eos non consectetur id quo. Voluptatem est voluptatem et.
- followers : 175
- following : 2800